New processes for cost-efficient solar cell production
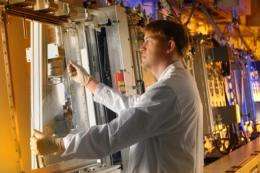
Many people answer with a resounding "yes!" when asked if they want environmentally-friendly solar cell-based power – though it should be inexpensive. For this reason, a veritable price war is raging among the makers of photovoltaic cells. Above all, it are the cheap products of Asian origin that are making life tough for domestic manufacturers. Tough, that is, until now: the researchers at the Fraunhofer Institute for Surface Engineering and Thin Films IST in Braunschweig are providing support to these companies. They are engineering coating processes and thin film systems aimed at lowering the production costs of solar cells drastically.
Scientists will exhibit a few of these new processes at the EU PVSEC trade show in Frankfurt from September 25 to 28 (Hall 03, Booth G22).
Hot wires instead of plasma
The photovoltaic industry is pinning its hopes particularly on high-efficiency solar cells that can achieve efficiencies of up to 23 percent. These "HIT" cells (Heterojunction with Intrinsic Thin layer) consist of a crystalline silicon absorber with additional thin layers of silicon. Until now, manufacturers used the plasma-CVD process (short for Chemical Vapor Deposition) to apply these layers to the substrate: the reaction chamber is filled with silane (the molecules of this gas are composed of one silicon and four hydrogen atoms) and with the crystalline silicon substrate. Plasma activates the gas, thus breaking apart the silicon-hydrogen bonds. The now free silicon atoms and the silicon-hydrogen residues settle on the surface of the substrate. But there's a problem: the plasma only activates 10 to 15 percent of the expensive silane gas; the remaining 85 to 90 percent are lost, unused. This involves enormous costs.
The researchers at IST have now replaced this process: Instead of using plasma, they activate the gas by hot wires. "This way, we can use almost all of the silane gas, so we actually recover 85 to 90 percent of the costly gas. This reduces the overall manufacturing costs of the layers by over 50 percent. The price of the wire that we need for this process is negligible when compared to the price of the silane," explains Dr. Lothar Schäfer, department head at IST. "In this respect, our system is the only one that coats the substrate continously during the movement – this is also referred to as an in-line process." This is possible since the silicon film grows up at the surface about five times faster than with plasma CVD – and still with the same quality of layer. At this point, the researchers are coating a surface measuring 50 by 60 square centimeters; however, the process can be easily scaled up to the more common industry format of 1.4 square meters. Another advantage: The system technology is much easier than with plasma CVD, therefore the system is substantially cheaper. Thus, for example, the generator that produces the electric current to heat the wires only costs around one-tenth that of its counterpart in the plasma CVD process.
In addition, this process is also suitable for thin film solar cells. With a degree of efficiency of slightly more than ten percent, these have previously shown only a moderate pay-off. However, by tripling the solar cells (i.e., by putting three cells on top of each other) the degree of efficiency spikes up considerably. But there is another problem: Because each of the three cells is tied to considerable material losses using the plasma CVD coatings, the triple photovoltaic cells are expensive. So the researchers see another potential use for their process: the new coating process would make the cells much more cost-effective. Triple cells could even succeed over the long term if the rather scarce but highly efficient germanium is used. However, germanium is also very expensive: in order for it to be a profitable choice, one must be able to apply the layers while losing as little of the germanium as possible – by using the hot-wire CVD process, for instance.
Saving 35 percent in the sputter process for transparent conductive oxide
The power generated by photovoltaic cells has to be able to flow out, in order for it to be used. To do so, usually a contact grid of metal is evaporated onto the solar cells, which conducts the resulting holes and electrons. But for HIT cells, this grid is insufficient. Instead, transparent, conductive layers – similar to those in an LCD television – are needed on the entire surface.
This normally happens through the sputter process: ceramic tiles, made from aluminum-doped zinc or indium-zinc oxide, are atomized. The dissolved components attach to the surface, thereby producing a thin layer. Unfortunately, the ceramic tiles are also quite expensive. Therefore, the researchers at IST use metallic tiles: They are 80 percent cheaper than their ceramic counterparts. An electronic control ensures that the metal tiles do not oxidize. Because that would otherwise change the manner in which the metal sputters. "Even though the control outlay is greater, we can still lower the cost of this production process by 35 percent for 1.4 square meter coatings," says Dr. Volker Sittinger, group manager at IST.
The research team intends to combine both processes over the long term, in order to make thin-coated solar cells more cost-effective and ultimately, more profitable. "You can produce all silicon layers using the hot-wire CVD, and all transparent conductive layers through sputtering with metal tiles. In principle, these processes should also be suitable for large formats," states Sittinger. However, the processes being used are not production processes quite yet: Even if the researchers already apply the processes to a countless number of square centimeters, it will still take about three to five years until they can be used in the production of solar cells.
Provided by Fraunhofer-Gesellschaft