First gasoline produced by bioliq pilot plant
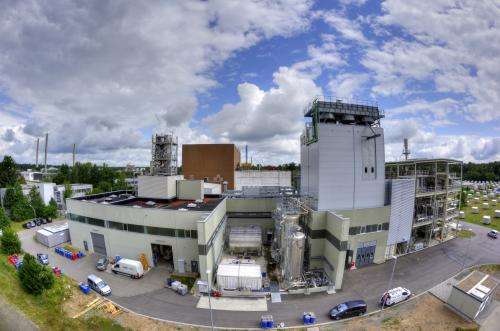
For the first time, gasoline is produced by Karlsruhe Institute of Technology (KIT). The synthesis stage of the bioliq pilot plant successfully started operation. Hence, KIT, in cooperation with Chemieanlagenbau Chemnitz GmbH, has progressed further in the production of environmentally compatible fuels from residual biomass. Now, all stages of the bioliq process, i.e. flash pyrolysis, high-pressure entrained-flow gasification, and synthesis, have been realized. The project will now be completed by testing the entire process chain and optimizing it for the large industrial scale.
As soon as all stages of the bioliq process will have been linked, the pilot plant will supply high-quality fuel from straw, probably in mid-2014. The four-staged bioliq process developed by KIT accounts for the fact that straw and other biogenous residues have a low energy density and arise in a widely distributed manner. Moreover, the bioliq process allows for the economically efficient large-scale production of high-quality engine-compatible designer fuels.
The bioliq synthesis stage now is the last section of the bioliq pilot plant on KIT Campus North to successfully start operation. Upstream of hot gas cleaning, the synthesis stage converts synthesis gas into high-quality Otto fuel based on two reaction steps. Plant design is specially adapted to CO-rich synthesis gas produced by gasification of sustainable biomass. Maximum utilization of the carbon contained in the biomass with a minimum investment volume is achieved by direct conversion of the synthesis gas into dimethyl ether in the first reaction step.
"The plant sections that have already started operation and the new synthesis stage of the bioliq pilot plant make up a unique demonstration plant at KIT," says KIT Vice President for Research and Innovation, Dr. Peter Fritz. "At the same time, bioliq is an excellent platform for research into the use of sustainable biomass for purposes other than food production." Professor Jörg Sauer, Head of the KIT Institute of Catalysis Research and Technology (IKFT), explains: "We can test new developments directly in the pilot plant on a scale relevant to industry. In this way, our research findings will be commercialized much more rapidly in the future." According to Joachim Engelmann, spokesman of the board of Chemieanlagenbau Chemnitz GmbH, interest of international clients in the bioliq process is high. "Successful cooperation with KIT is of major strategic importance to our future," Engelmann says.
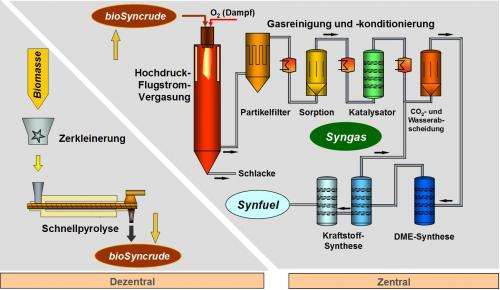
Setup of the pilot plant on KIT Campus North was funded by the federation, the state of Baden-Württemberg, and the EU. Apart from numerous institutes and service units of KIT, several industry partners are involved in the bioliq project.
Construction of the bioliq synthesis stage has an investment volume of about EUR 22 milion. 50 percent were financed by the Federal Ministry of Food, Agriculture, and Consumer Protection (BMELV) and from the European Regional Development Fund (ERDF). The BMELV funds were provided via the Fachagentur Nachwachsende Rohstoffe e.V. (FNR, Agency for Renewable Resources), the ERDF funds via the Baden-Württemberg Ministry of Economics. The remaining investment costs are borne by KIT and its industry partner Chemieanlagenbau Chemnitz GmbH. The latter projected, delivered, assembled, and commissioned the bioliq® synthesis stage. Under a joint cooperation contract, it will also participate in future research and development work as a partner of KIT.
The bioliq Process
The complete bioliq process (Biomass to Liquid Karlsruhe) comprises four stages. In the first stage, the dry residual biomass that arises in a widely distributed manner and possesses a low energy content is subjected to decentralized conversion by flash pyrolysis into a substance of high energy density similar to crude oil. This substance, the so-called bioliqSynCrude, can be transported over long distances in an economically efficient manner and is subjected to further central processing. A high-pressure entrained flow gasifier converts the bioliqSynCrude® to a tar-free syngas at temperatures above 1200°C and pressures of up to 80 bar. This synthesis gas is mainly composed of carbon monoxide and hydrogen. By means of downstream hot gas cleaning, impurities like particular matter, chlorine and nitrogen compounds are separated from the syngas. In the synthesis stage, this synthetic gas is specifically composed to high-quality fuels.
Provided by Karlsruhe Institute of Technology