Drive system saves space and weight in electric cars
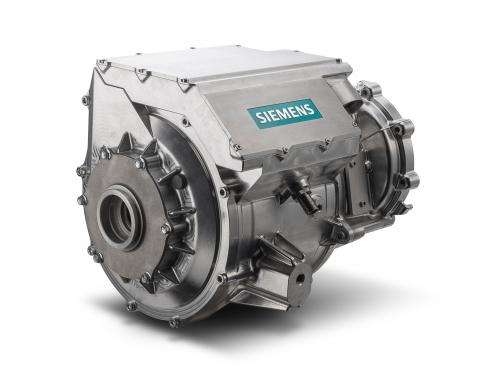
Siemens has developed a solution for integrating an electric car's motor and inverter in a single housing. Until now, the motor and the inverter, which converts the battery's direct current into alternating current for the motor, were two separate components. The new integrated drive unit saves space, reduces weight, and cuts costs. The solution's key feature is the use of a common cooling system for both components. This ensures that the inverter's power electronics don't get too hot despite their proximity to the electric motor, and so prevents any reduction in output or service life.
Because range is a decisive criterion for purchasing an electric car, automakers are always striving to reduce vehicle weight. This was also the aim of the Siemens engineers. Their idea was to integrate the inverter into the motor, as this would reduce weight because only a single housing would be needed. In addition, it would create six to seven liters of additional installation space, which could be used for a charging unit, for example. Integration would also eliminate the costs of wiring the motor to the inverter and fewer assembly steps would be needed to produce the vehicle.
Cooling is key
Siemens developed the integrated drive unit Sivetec MSA 3300 on the basis of a series electric motor. The engineers adapted the housing in such a way that the inverter could be integrated into the motor. One problem they faced was the heat generated by the electric motor. At high temperatures, the output of the IGBT modules - the high-performance semiconductors that convert the battery's current into alternating current - has to be limited. For this reason, inverters in electric cars. always have their own water cooling system. Another component of the overall solution is the very robust power modules featuring SkiN technology. SkiN is a bonding technology that connects the surface of the semiconductor chip without requiring bonding wire. When the thermal load fluctuates, the electrical contact between the chip and the bonding wire is a weak point of semiconductor components.
A key feature of the integrated drive unit was therefore the creation of a special cooling water system around the motor and inverter. The coolest water first flows around very thermally sensitive components such as the IGBT modules and the intermediate circuit capacitor, after which it is led into the motor's cooling jacket. The water flow system is designed in such a way that a kind of water screen is created between the inverter electronics and the motor. As a result, it thermally isolates the two units from one another.
The concept's feasibility has already been demonstrated in a lab under the typical load curves and operating conditions of an electric motor in an automobile. The industry has expressed considerable interest in Sivetec MSA 3300, and the system was recently nominated for the eCarTec Award 2014, which is the Bavarian State Award for Electric and Hybrid Mobility.
Provided by Siemens