Starving the energy monster for energy efficient buildings
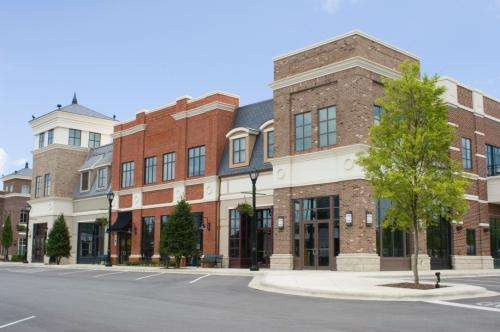
There are one and a half million commercial buildings in the U.S. Less than ten percent of them have energy management systems. Technology from a Siemens company in Austin, Texas has what it takes to steadily ramp down this huge sector's appetite for energy.
Although high-profile measures to slow global warming seem to be eternally stuck in neutral, a combination of technology and market forces offers the potential of putting a significant dent in energy demand and carbon dioxide emissions in the United States. According to a 2009 McKinsey report entitled "Unlocking Energy Efficiency in the U.S. Economy," the commercial sector, which includes everything from office and retail buildings to hotels, restaurants and warehouses, will account for 20 percent of all the energy used in the U.S. by 2020, or about 20 quadrillion BTUs of primary energy.
Cutting energy bills
But even as average energy demand per square foot continues to grow at 1.5 percent per year throughout this vast sector, customers of Austin, Texas-based Siemens company Retail & Commercial Systems (RCS), which provides enterprise-level energy management for chains of mid-sized retail facilities such as health clubs, supermarkets and branch banks, are demonstrating that a completely different course is possible.
In spite of the rising cost of energy, their electric bills have steadily headed south—typically between 15 and 30 percent over a 28- to 36-month period, resulting in an extremely rapid return on investment. Seeing a perfect match with its market-leading position in the automation and energy optimization of very large buildings such as hospitals, office towers and stadiums, Siemens Building Technologies (SBT) acquired the Austin company—then known as Site Controls—in late 2010.
Now, RCS is helping a wide range of customers with sites across the United States and Canada not only to reduce their energy bills, but to hone their facility intelligence and come up with smart grid solutions.
Intensive care for stores
RCS specializes in chains of stores in which the buildings are essentially the same. In each case, it outfits the heating and cooling units in customer facilities with sensors designed to continuously monitor equipment performance, equips customer areas with wall-mounted carbon dioxide sensors as a proxy for occupancy detection—a key parameter in determining how much cooling is needed on a real-time basis—and connects thermostats and lighting controls to a control box with its own Linux-based computer and embedded Web server. Depending on the customer, other major systems such as refrigeration units, trash compactors, signage, rooftop solar power equipment, and electric vehicle charging stations can also be equipped with sensors.
Each store's control box interrogates its sensors every sixty seconds and delivers a condition report to the chain operator's headquarters every two hours.
What's more, every four hours, a cloud-based RCS data management center generates a prioritized list of the specific systems in a chain operator's entire fleet of stores that require immediate service. "It's like monitoring patients in an intensive care unit," says RCS General Manager Marcus Boerkei. "Our software keeps an eye on each store's energy-related vital signs, identifies equipment that is not operating at specified levels, prioritizes problems, and generates actionable information that focuses the customer's attention on those stores that need help."
Enterprise-wide overview
Adds RCS Business Development Director Dan Kubala, "Until we came to this market, no one had the tools to do this sort of thing. Typically, our customers have a number of cooling units on the roof, all supplying a common sales area—think 'big box' store. If one malfunctions, it may actually be pumping hot air into a store, forcing the other units to work even harder. But without the ability to automatically identify such situations, no one notices, except that energy bills just keep climbing." Even worse, he says, are technicians who go to the roof, do little or nothing, and bill a store for their services. "Without remote sensing, there is no mechanism to verify whether a job was actually done," he says.
Continuous data harvesting
Careless store managers can also be a problem. "What we absolutely want to avoid," says Kubala, "is the manager who turns the thermostat down to 66 on a hot day and then leaves it there for the entire summer. With our system, corporate energy managers receive regular updates on temperature settings across their entire enterprise, enabling them to prevent this behavior." In view of these and other causes of locally-induced energy waste, RCS software allows headquarters to set each store's temperature and lighting levels and coordinate these levels with store operating hours, weekend and holiday peaks, and seasonal changes. What's more, as RCS learns from best practices, it remotely deploys new, customer-approved capabilities across the entire enterprise as a free service.
Thanks to cloud-based data management and continuous data harvesting, RCS software also helps chain operators to, for instance, identify which cooling systems work best in which climates, and which ones have the best service and efficiency records. "All of this information helps to optimize functions in existing facilities, and supports the planning of new facilities," says Boerkei. "It also allows a customer to look at fleet performance, compare it year on year, and even compare how his fleet is doing compared to the industry average in real time."
Toward virtual power plants
In addition to steadily driving down chain operators' energy costs and providing business intelligence, RCS helps its customers to make the most of oscillating electricity prices and receive cash from utilities for reducing electricity demand during peak periods. The company's SureGrid intelligent load management (ILM) technology, which is a standard part of its solution, "essentially turns a building into a fully automated system that can shed demand in response to market signals from a utility," says Boerkei. "If, for instance, the price per kWh jumps from 6 cents to 13 cents, the building can power down a range of functions that have previously been agreed to by the customer depending on circumstances."
As RCS adds more and more buildings to the thousands it already controls, the aggregate effect of reduced demand can have a significant impact on local utilities. Incentivized by contracts that pay utility customers for each kW they shed below a predefined minimum, so many buildings already participate that utilities are able to avoid switching on so-called peaking plants. "The result is that aggregations of RCS-equipped buildings participating in a demand-response event start to look like virtual power plants," says Boerkei. Normally, however, some buildings would be unable to reduce demand—think of a popular restaurant on a Friday night, for instance—and would be penalized with very high electricity prices. With this in mind, RCS bids the aggregate load of its buildings to the utility. "That way the individual site can do what it needs to do. It's like a diversified stock portfolio," says Boerkei. "We negotiate with our customers and split the rewards." As RCS expands into more and more chains of buildings, there are likely to be plenty of rewards—particularly for the environment.
Provided by Siemens