Engineers cut time to 3D-print heterogeneous objects from hours to minutes (w/ Video)
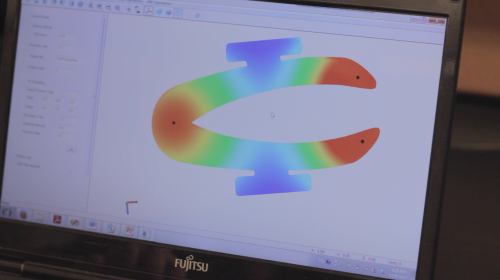
Researchers at the USC Viterbi School of Engineering have developed a faster 3D printing process and are now using it to model and fabricate heterogeneous objects, which comprise multiple materials.
Although 3D printing – or direct digital manufacturing – has the potential to revolutionize various industries by providing faster, cheaper and more accurate manufacturing options, fabrication time and the complexity of multi-material objects have long been a hurdle to its widespread use in the marketplace. With this newly developed 3D printing process, however, USC Viterbi professor Yong Chen and his team have shaved the fabrication time down to minutes, bringing the manufacturing world one step closer to achieving its goal.
"Digital material design and fabrication enables controlled material distributions of multiple base materials in a product component for significantly improved design performance. Such fabrication capability opens up exciting new options that were previously impossible," said Yong Chen, Ph.D., professor in the Daniel J. Epstein Department of Industrial and Systems Engineering and the study's lead researcher.
Traditional modeling and prototyping approaches used to take days, but over the past several decades various additive manufacturing (AM) processes have been developed to fabricate both homogeneous and heterogeneous objects more quickly. Currently, AM processes such as multi-jet modeling, which create a solid 3D object from a digital model by laying down successive layers of material, can fabricate a complex object in a matter of hours.
Last year, Chen and another team of USC Viterbi researchers improved an AM-related process called mask-image-projection-based stereolithography (MIP-SL) to drastically speed up the fabrication of homogeneous 3D objects. In the MIP-SL process, a 3D digital model of an object is sliced by a set of horizontal planes and each slice is converted into a two-dimensional mask image. The mask image is then projected onto a photocurable liquid resin surface and light is projected onto the resin to cure it in the shape of the related layer.
Furthermore, the USC Viterbi team developed a two-way movement design for bottom-up projection so that the resin could be quickly spread into uniform thin layers. As a result, production time was cut from hours to a few minutes. In their latest paper, the team successfully applies this more efficient process to the fabrication of heterogeneous objects that comprise different materials that cure at different rates. This new 3D printing process will allow heterogeneous prototypes and objects such as dental and robotics models to be fabricated more cost- and time-efficiently than ever before.
In future work, Chen and his team will investigate how to develop an automatic design approach for heterogeneous material distribution according to user-specified physical properties and how to improve the fabrication speed.
Chen and USC Viterbi industrial and systems engineering doctoral candidates students Pu Huang and Dongping Deng are presenting their findings at ASME's 2013 International Mechanical Engineering Congress and Exposition in San Diego on November 20th.
Provided by University of Southern California