Production of fiber reinforced plastic components without release agents
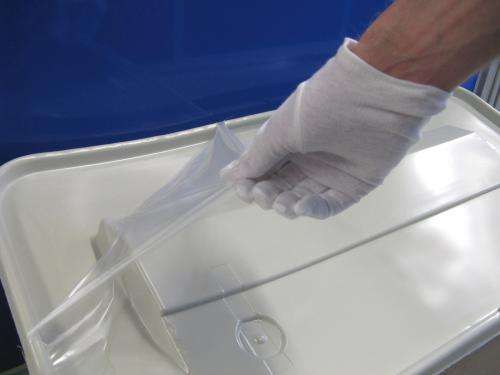
Up to now, releasing components from molds has called for release agents. The problem is that the residues of these agents left behind must then be costly removed. Now, there is an alternative: a specially coated release film that leaves no residues.
If you want to bake a cake, you have to grease the baking pan beforehand; otherwise the cake will stick to it. Making fiber reinforced plastic components (FRP components) is much the same: release agents are wiped or sprayed onto the surface of the mold so that the component can be taken out once it was cured. However, this approach leaves behind residues of release agents on both the component and the mold. Component surfaces must usually then be manually cleaned – a painstaking and potentially critical process, since removing too much material has a negative impact on component quality. Molds, too, must be regularly cleaned – but the downtime entails a not insignificant price. Now, the Fraunhofer Institute for Manufacturing Technology and Advanced Materials IFAM has developed a release film that renders these cleaning tasks. "Our film can be applied to structures of all kinds and makes it easy to release components from molds," says Dr. Matthias Ott, project manager in the Plasma Technology and Surfaces PLATO section. "It features a 0.3 micrometer thick plasma-polymer release layer that leaves no residues on the surface of the component."
This coating on the film is based on development work conducted at the IFAM on producing non-stick component molds using a low-pressure plasma process. First, the mold to be coated is placed in a plasma reactor and atmospheric pressure is reduced to one 10,000th. Next, layering gases are fed into the reactor and a plasma is ignited. Molecules containing silicon or carbon that are injected into the plasma are deposited as a thin layer. Since the molecules are highly reactive, they bond very well with the mold.
Up to 300 percent elasticity
But there's a snag: plasma reactors are at best five cubic meters in volume, which means only relatively small molds can be coated. So the researchers in Bremen, together with experts from Fraunhofer IFAM's Project Group Joining and Assembly FFM in Stade, decided to strike out in a new direction. "We wanted to make the process available for big components too, for instance in aircraft manufacturing, by means of an appropriate release film," says Dipl.-Ing. Gregor Graßl, FFM project manager. While release films are already commercially available, they are very stiff. This means they cannot be deep drawn and are suited only to simple mold contours. The IFAM scientists, on the other hand, are using a film that while tough also demonstrates up to 300 percent elasticity. What's more, at less than 0.1 millimeters it is extremely thin. "That means it can also be applied to curved or structured surfaces without creasing," says Graßl.
The challenge that had to be overcome was how to get the coating to stick to the film. "We developed a plasma process which relaxes the release layer. Put another way, the layer enters a state of equilibrium as soon as the plasma is turned off and no more highly reactive particles are formed, and the molecules it contains then organize themselves such that the surface no longer exhibits any reactive groups," explains Ott. As a result, the resin of the composite part does not bond with the release layer, but the release layer bonds very well with the film – not detaching even when subjected to forces such as extreme stretching. In contrast to the films available to date, this new film leaves no residues of release agents on FRP components. "We are using what amounts to a new class of materials that, by virtue of their chemical structure, are harder than classic polymers," says Ott.
This film, known as FlexPLAS, has already demonstrated that it can cope with real-life production demands in the FFM development hall. It is currently being tested by a number of customers.
Provided by Fraunhofer-Gesellschaft