Mechanical engineer investigates passive cooling system for microelectronics
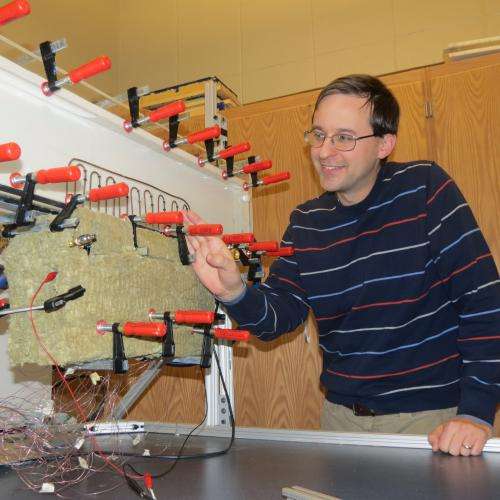
On a cold February day, heat is a good thing, but not when it comes to electronics. Assistant professor Gregory Michna of the SDSU Mechanical Engineering Department is developing a means of cooling laptops and portable electronic devices more efficiently.
He is investigating tiny flexible pipes that can cool a device while using a minimum amount of power. It's called a pulsating or oscillating heat pipe cooling system.
"It can move a lot of heat without a power input and is cheaper to manufacture than traditional heat pipes," Michna explained. Current cooling systems use fluid-filled copper piping with a wick structure along with a fan called a heat pipe.
When it comes to computing power, "heat rejection is a limiting factor," Michna said. "Conventional cooling methods are not adequate for the faster, small processors being developed."
Through a one-year, $99,118 grant from the South Dakota Board of Regents, Michna will evaluate the pulsating system's operation during startup and ways to miniaturize the cooling portion to fit in a small heat sink. Graduate student Sagar Paudel of Nepal and undergraduate student Mitchell Hoesing of Jackson, Neb., are working on the project with Michna.
Reducing power demand
With the pulsating heat pipe, a single tube loops up and down accordion-style from the hot to the cool part of the device, he explained. "The idea is to capture heat on one end and release it on the other."
This capillary system does not require a wick structure and is partially filled with a working fluid. Used in combination with a heat sink, the fluid vaporizes when it absorbs heat in the hot section and then condenses as it releases heat in the cool portion, Michna explained.
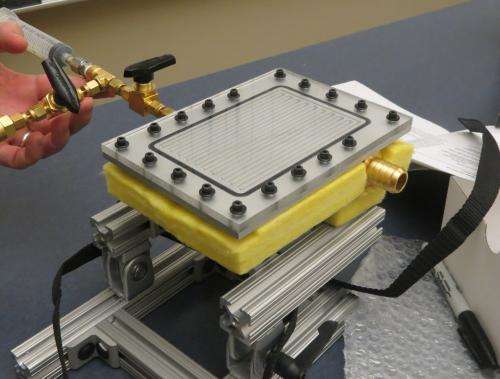
When the temperature difference between the hot and cool ends exceeds a certain threshold, the fluid begins to oscillate in the thin tube. Thus, the passive system "doesn't draw power," Michna explained. The design's simplicity increases its reliability and decreases its cost.
However, these oscillations are driven by instability, which makes modeling the process difficult. Michna and his team will try to figure out which parameters affect performance the most.
To perform testing, Michna and his students have built two experimental devices—one large and another small.
Both currently use water, but the working fluid could also be alcohol or refrigerant.
One of the questions Michna wants to answer is whether the pulsating system will allow the temperature of the electronic device to get too high initially before the system begins cooling. The data his team gathers will strengthen an upcoming proposal to the National Science Foundation.
When it comes to developing smaller, more powerful electronic devices, Michna noted that "thermal management is a limiting factor. It's all about reliability, keeping temperatures low and consistent."
Pulsating heat pipes could have a heat transfer capacity up to 100 times better than conventional heat pipes, Michna explained. "This will allow the use of more high-powered electronics in more places."
Provided by South Dakota State University