Researchers develop revolutionary 3D printing technology
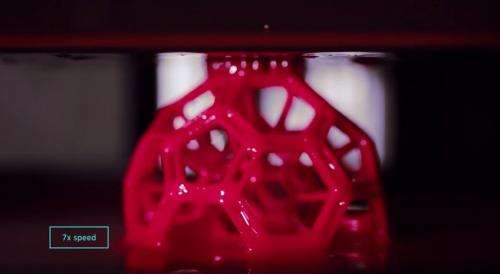
A 3D printing technology developed by Silicon Valley startup, Carbon3D Inc., enables objects to rise from a liquid media continuously rather than being built layer by layer as they have been for the past 25 years, representing a fundamentally new approach to 3D printing. The technology, to appear as the cover article in the March 20 print issue of Science, allows ready-to-use products to be made 25 to 100 times faster than other methods and creates previously unachievable geometries that open opportunities for innovation not only in health care and medicine, but also in other major industries such as automotive and aviation.
Joseph M. DeSimone, professor of chemistry at UNC-Chapel Hill and of chemical engineering at N.C. State, is currently CEO of Carbon3D where he co-invented the method with colleagues Alex Ermoshkin, chief technology officer at Carbon 3D and Edward T. Samulski, also professor of chemistry at UNC. Currently on sabbatical from the University, DeSimone has focused on bringing the technology to market, while also creating new opportunities for graduate students to use the technique for research in materials science and drug delivery at UNC and NCSU.
The technology, called CLIP - for Continuous Liquid Interface Production - manipulates light and oxygen to fuse objects in liquid media, creating the first 3D printing process that uses tunable photochemistry instead of the layer-by-layer approach that has defined the technology for decades. It works by projecting beams of light through an oxygen-permeable window into a liquid resin. Working in tandem, light and oxygen control the solidification of the resin, creating commercially viable objects that can have feature sizes below 20 microns, or less than one-quarter of the width of a piece of paper.
"By rethinking the whole approach to 3D printing, and the chemistry and physics behind the process, we have developed a new technology that can create parts radically faster than traditional technologies by essentially 'growing' them in a pool of liquid," said DeSimone, who revealed the technology at a TED talk on March 16 in the opening session of the conference in Vancouver, British Columbia.
Through a sponsored research agreement between UNC-Chapel Hill and Carbon 3D, the team is currently pursuing advances to the technology, as well as new materials that are compatible with it. CLIP enables a very wide range of material to be used to make 3D parts with novel properties, including elastomers, silicones, nylon-like materials, ceramics and biodegradable materials. The technique itself provides a blueprint for synthesizing novel materials that can further research in materials science.
Rima Janusziewicz and Ashley R. Johnson, graduate students in DeSimone's academic lab, are co-authors on the paper and are working on novel applications in drug delivery and other areas.
"In addition to using new materials, CLIP can allow us to make stronger objects with unique geometries that other techniques cannot achieve, such as cardiac stents personally tailored to meet the needs of a specific patient," said DeSimone. "Since CLIP facilitates 3D polymeric object fabrication in a matter of minutes instead of hours or days, it would not be impossible within coming years to enable personalized coronary stents, dental implants or prosthetics to be 3D printed on-demand in a medical setting."
CLIP's debut coincides with the United Nation designating 2015 as the International Year of Light and Light-Based Technologies, which recognizes important anniversaries of scientific advances enabled with light.
More information: Continuous liquid interface production of 3D objects, Published Online March 16 2015. Science DOI: 10.1126/science.aaa2397
Journal information: Science
Provided by University of North Carolina at Chapel Hill