Better protection for forging dies
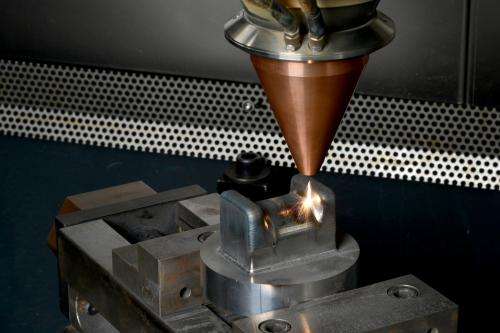
Hard or tough - very often, the manufacturers of forging dies must make a compromise here. A new technology now makes it possible to combine both characteristics and clearly expand the useful life of forging dies. The scientists will introduce the process at the Euromold trade fair, from Nov. 27 - 30 in Frankfurt, Germany.
Forging dies must withstand a lot. They must be hard so that their surface does not get too worn out and is able to last through great changes in temperature and handle the impactful blows of the forge. However, the harder a material is, the more brittle it becomes - and forging dies are less able to handle the stress from the impact. For this reason, the manufacturers had to find a compromise between hardness and strength. One of the possibilities is to surround a semi-hard, strong material with a hard layer. The problem is that the layer rests on the softer material and can be indented by blows, like the shell of an egg.
Researchers from the Fraunhofer Institute for Production Technology IPT in Aachen, Germany have now developed an alternative. "The forging dies we have been working on have a useful life that is up to twice as long," explains Kristian Arntz, head of department at the IPT. "We are using a working material that is less hard and able to handle the impact stress well. We melt the uppermost layer of the material with a laser and introduce a powder into the melt material that is used to chemically alter the characteristics of the material. We have therefore achieved a large degree of hardness in the upper millimeter." The advantage is that since the characteristics of the outer layer do not change abruptly (as is the case in a deposited layer), but increases in hardness gradually (this is also called a hardness gradient) we can circumvent the "egg shell effect". In addition, the particles act like sand paper and prevent the material from wearing off the die. Since the wear only occurs in certain spots of the die, the scientists are very targetedly altering only these surface areas. They are therefore further minimizing the effect the layer has on the impact resistance. Simulations help to calculate the areas that are particularly stressed – and knowledge gained by experience is also applied.
To be able to work on the forging dies, the scientists and their colleagues at Alzmetall have developed a machine with which they are able to work on the free-form die inserts and forging dies. The scientists have also developed a software with ModuleWorks that ensures that the laser travels across the surface at a constant speed and that the gaps between the laser paths remain even – otherwise tears would develop in the surface. "This isn't a problem if the surfaces are straight; however, we had to develop special algorithms for free-formed tools that keep the path distance and the speed constant – even with complex geometries," said Arntz. The machine and the software are ready; the scientists have already manufactured initial tools and dies for the industry. They will introduce the technology at the Euromold trade fair (Hall 11, Booth C66) from November 27 - 30 in Frankfurt, Germany.
The scientists are planning, in a further step, to reduce expensive raw materials such as chromium, molybdenum and vanadium. To date, these materials are present in all forging dies. "We want to utilize the basic fundamentals of our technology so that we only have to alloy the reworked surface layer with these materials."
Provided by Fraunhofer-Gesellschaft