Adding precision to plastics testing
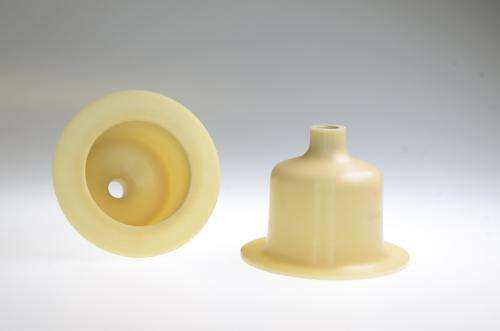
Plastics play an important role in many consumer items. But testing precisely how much load these plastic parts can bear has up to now been a very complicated task. Now, a new instrument achieves simpler and more accurate measurements.
So that relaxed Sunday outing came to nothing. The car broke down after just a few kilometers. Why? Because a tiny crack in the gasoline pump brought the engine to a standstill. An operating life of several thousand hours proved to be too much for the plastic component to take. To keep occurrences of this kind rare, specialists regularly put important plastic components to the test. As a material, plastic's importance goes way beyond cars: it's plastic that keeps our washing machines running, makes sure the coffee that comes out of the machine tastes good, keeps our drainpipes clean, and guarantees that insulating materials don't fail – among many, many other applications. There's just about no end to where plastics are used.
Given that every component reacts completely differently to stresses, it's a tricky business to obtain exact test results. In an effort to keep the workload down to a manageable level, researchers get representative results from a test piece made using the same material, as opposed to testing individual components. Dominik Spancken of the Fraunhofer Institute for Structural Durability and System Reliability LBF in Darmstadt describes the typical approach: "Generally our customer provides us with a certain quantity of plastic granulate, which is the base material for plastic products. We use this granulate to create test pieces and subject these to various loads. Our computers record the values and calculate a lifecycle model for each material." The drawback with this approach is that researchers can only ever study one spatial load at a time, for instance pressure or strain at a single point. But in fact plastic components are mostly subjected to loads along multiple axes – in other words, they are maltreated from all sides. "That's why measurements were often just an approximation," says Spancken of this dilemma.
Water pressure simulates loads
The most realistic way to simulate the loads that plastics are subjected to is with the internal pressure process. This uses a special piece of equipment to press a fluid medium – perhaps water, oil or brine – against the walls of the test piece from within. This simulates an even distribution of pressure. The problem is it wasn't possible to apply this process with the equipment available up to now when the test pieces were solid. So the researchers had to redesign the test piece, the process and the testing equipment. And the result is the MultiTester, a hollow thermoplastic object that looks a little like a bell jar you might put over cheese. Straightforward to produce by injection molding, it can easily be adjusted to a wide range of test scenarios. Wall thickness, environmental influences and load types can for instance all be set to any desired value. What is more, the scientists can determine the degree of influence that reinforcing fibers have. "These special materials can usually cope with double the pressure," describes Spancken.
This new method complements existing test scenarios, which are still used to come up with initial predictions of a given component's load behavior. The MultiTester validates the data collected and defines load limits with even more precision. Anyone wanting to take a closer look at the new test piece should visit the Composites Europe trade fair, which is being held in Stuttgart from September 17 – 19, where the LBF will be presenting this technology to the public for the first time in Hall 6, Booth A02.
Provided by Fraunhofer-Gesellschaft