Perfectly non-reflecting
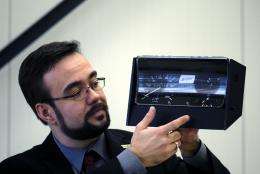
(PhysOrg.com) -- A new nanocoating ensures a perfectly non-reflecting view on displays and through eyeglasses. The necessary surface structure is applied to the polymeric parts during manufacture, obviating the need for a separate process step. The hybrid coating has further advantages: the components are scratch-proof and easy to clean.
Moths are the prototype. As they search for food at dusk they have to hide from predators. Their presence must not be betrayed by reflections on their facet eyes. On other insects these eyes shimmer, but the moth’s eyes are perfectly non-reflecting. Tiny protuberances smaller than the wavelength of light form a periodic structure on the surface. This nanostructure creates a gentle transition between the refractive indices of the air and the cornea. As a result, the reflection of light is reduced and the moth remains undetected.
German research scientists at the Fraunhofer Institute for Mechanics of Materials IWM in Freiburg have adopted this artifice and adapted it to a range of different applications. On eyeglasses, cell phone displays, fitting or panel covers, transparent surfaces are generally only useful if they allow viewing without light reflecting back. Whereas conventional methods apply the anti-reflective coating in a separate step after production, the Fraunhofer scientists have found a way of reducing light reflection during actual manufacture of the part or component: "We have modified conventional injection molding in such a way that the desired nanostructure is imparted to the surface during the process," explains Dr. Frank Burmeister, project manager at the IWM.
For this the researchers have developed a hard material coating which reproduces the optically effective surface structure. "We use this to coat the molding tools," says Burmeister. "When the viscous polymer melt is injected into the mold, the nanostructures are transferred directly to the component." Because no second process step is required, manufacturers achieve an enormous cost saving and also increase efficiency. "Normally the component would have to undergo an additional separate process to apply the anti-reflex coating," Burmeister adds.
Normal plexiglass and some anti-reflex coatings are particularly sensitive, but the scientists are producing wipe-resistant and scratch-proof surfaces. For this purpose the injection mold is additionally flooded with an ultra-thin organic substance made of polyurethane. Burmeister: "The substance runs into every crevice and hardens, like a two-component adhesive." The result is an extremely thin nanocoating of polyurethane on which the optically effective surface structures, which are just one ten-thousandth of a millimeter thick, are also reproduced. Working in cooperation with industrial partners, the research scientists now aim to develop components for the auto industry, for example, which are not only attractive to look at but also hard-wearing and easy to clean.
Provided by Fraunhofer-Gesellschaft