Laser image aimed at achieving 85 percent reduction in costs
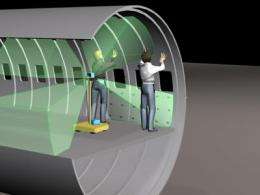
An innovative laser imaging technique, developed with funding from the Office of Naval Research (ONR), could cut more than 7,700 man hours from the manufacturing cycle of the VIRGINA-Class Submarine (VCS).
Per submarine, the savings could reach $500K per hull, translating in a projected savings of $15.5M over a 31-hull construction program.
Successfully piloted in June 2008, the laser image projection technology allows the Quonset Point, R.I., Electric Boat (EB) manufacturing facility to automate the layout of attachments during the early outfitting stages of the VCS. This automation could result in an estimated 85 percent reduction in labor over the current method.
The laser imaging technology uses 3-D digital ship design data generated by the OneStop CAD database. OneStop extracts positional data from the EB product model to determine the quantity and specific location of various attachments.
The EB project team cut its dependency on paper templates and string measurements using OneStop. In fact, the team located and attached 4,822 electrical and ventilation hangers, and installed approximately 8,862 studs in 21 of the 22 VCS hull cylinders during the pilot program.
The laser image projection technology will ultimately equip production workers with direct access to the CAD model information needed to locate/mark points of attachment.
The EB project team continues to evaluate additional uses for the technology, and in future pilots will include attachment points for piping, sound damping and other fixed point attachments. The cylindrical shape of the submarine's hull is ideally suited to this technology, but other ship construction applications are also being considered and could result in cost savings for other Navy construction programs.
ONR's Navy Manufacturing Technology (ManTech) Center for Naval Shipbuilding Technology (CNST) sponsored the pilot. CNST is a Navy ManTech Center of Excellence, chartered by ONR to identify, develop and deploy, in U.S. shipyards, advanced manufacturing technologies in U.S. shipyards that will reduce the cost and time to build and repair Navy ships.
ManTech sponsorship is making a huge impact here at our QP facility," said Danielle Fernholz, point manager at the EB's Quonset Point facility. "We can't thank [ONR] enough for the tremendous opportunities this program is affording us."
Previous ManTech efforts on the VCS are projected to reduce design and engineering costs by $3.65M per year, generate a per-hull savings of $5.275M, reduce production cycle time from 84 to 60 months and enable the acquisition of two submarines per year. Known as Design for Production (DfP), these efforts have yielded an optimized design and production environment for the VCS and are applicable across the shipbuilding and weapons systems industries.
Source: Office of Naval Research