No Pulp Fiction: Engineers See Major Paper Mill Savings With New Rotor Technology
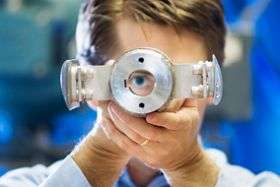
(PhysOrg.com) -- A partnership between University of British Columbia, government and the pulp and paper industry has resulted in the development of three high efficiency pulp screen rotors that produce high quality paper while reducing almost half the energy required.
“There are currently 300 pulp screens in British Columbia’s 20 pulp and paper mills,” says UBC Mechanical Engineering Assoc. Prof. James Olson. “The industry consumes almost 20 per cent of all the electricity produced in the province and pulp screening is an energy intensive operation in that process.”
Pulp screens work somewhat like the spin cycle in a household washing machine by rotating at high speeds and forcing pulp through narrow openings in the screen. Pulp screens in B.C. alone consume 300 Gigawatt Hours per year at an estimated cost of $16 million -- or enough energy to light up 15,000 homes.
Olson and fellow UBC engineers Carl Ollivier-Gooch and Mark Martinez, along with industrial partners at Montreal-based Advanced Fiber Technologies Inc., took inspiration from aerospace technology and designed a family of uniquely shaped, hydrodynamic rotors that significantly reduce drag and operate at much lower speeds and power, while increasing the capacity and efficiency of the screen.
The technology was patented and licensed to Advanced Fiber Technologies and 100 new rotors were installed in 30 mills across Canada.
“The trial results were beyond everyone’s expectations -- reducing electricity consumption by 52 per cent compared to current state-of-the-art rotors,” says Olson. “If all pulp screens used in B.C. mills were converted to the new rotor technology, an estimated $8 million could be saved each year. Adopted nation-wide, the industry could save $20 million a year.”
While the cost savings would increase the industry’s competitiveness against new paper producers such as China, the reduced energy usage also translates into lower greenhouse emissions. The new technology could also cement Canada’s leadership in pulp equipment manufacturing and further diversify a sector that currently logs $53 billion in sales and $44 billion in exports per year.
As a result of the success in the mill trials, the research team has won BC Hydro’s New Technology of the Year Award (2007), the Natural Sciences and Engineering Research Council of Canada (NSERC)’s Synergy Award for Partnership and Innovation (2007), and the British Columbia Innovations Council’s Lieutenant Governor’s Award (2008).
The work has also led to a $2.2 million investment from the Natural Sciences and Engineering Research Council of Canada and a partnership with 11 industry partners including BC Hydro and most of the paper mills in B.C.
“There’s a gap between electricity supply and demand in B.C. and we need to do more to conserve power,” says Lisa Coltart, BC Hydro’s director of Power Smart. “We’re excited to contribute to research that will provide substantial energy savings while making the province a world leader in the field.”
Provided by University of British Columbia