Plastic as a conductor
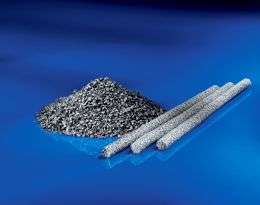
(PhysOrg.com) -- Plastic that conducts electricity and metal that weighs no more than a feather? It sounds like an upside-down world. Yet researchers have succeeded in making plastics conductive and cutting production costs at the same time.
You could hardly find greater contrasts in one and the same team. Plastic is light and inexpensive, but insulates electric current. Metal is resilient and conducts electricity, but it is also expensive and heavy. Up to now, it has not been possible to combine the properties of these two materials.
The IFAM in Bremen (Germany) has devised a solution that combines the best of both worlds without requiring new machinery to process the components. The greatest challenge for the researchers was getting the plastic to conduct electricity, for plastic-metal hybrids are to be used in the very places where plastic components are equipped with printed circuit boards, for instance in cars or aircraft. Until now, this was only possible via the roundabout route of punching and bending metal sheets in an elaborate process in order to integrate them in a component.
The new solution is simpler: a composite material. The different materials are not merely slotted together or bonded, but mixed in a special process to form a single material. This process produces a homogeneous and fine-meshed electrically conductive network. The composite possesses the desired chemical stability and low weight, coupled with the electrical and thermal conductivity of metals. As it will no longer be necessary in future to integrate metal circuit boards and the components will soon be able to be produced in a single work step, the production costs and the weight of the material are drastically reduced.
Automobile and aircraft manufacturers, in particular, will benefit from this development. The headlamp housings on a car, for example, are made of plastic. Until now, punched metal sheets have been installed in order to illuminate the headlamps. If the housings were fitted with circuit boards made of the conductive plastic-metal hybrids, they could be produced more efficiently and at lower cost than ever before. Many components of an aircraft, such as the fuselage, are partly made of carbon fiber composites (CFC). However, they lack the ability to conduct electricity. A stroke of lightning would have fatal consequences. A plastic-metal hybrid would be a good alternative for discharge structures on components.
Provided by Fraunhofer-Gesellschaft