Engineering students use smart materials to design a smart wing
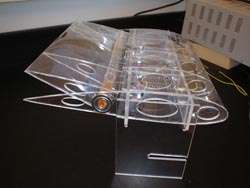
A prototype aircraft wing, designed last year by four Temple mechanical engineering seniors to use “memory alloys” and electrical current to control and position the wing’s flaps, was a finalist in the recent Collegiate Inventors Competition, a program of the National Inventors Hall of Fame Foundation and co-sponsored by the Abbott Fund and the U.S. Patent and Trademark Office.
The students, Jinho Kim, Charlie Hanna, Andrew Guion and Noah Heulitt, conceived the idea and built a model of the “smart wing” last year as part of their senior design project for the College of Engineering, where it won the Ridenour Prize for best mechanical engineering senior project.
Their work also will be published in the journal “Aircraft Engineering and Aerospace Technology” in January 2008.
“A conventional aircraft wing uses hydraulics and an electronic motor to move the flaps into their proper positions for ascent and descent, so it is very heavy and noisy,” said Kim, who is now a graduate student in Temple’s engineering program. “We replaced those with these ‘smart materials’ that we can manipulate through applied heat using electrical current.”
The students used two springs made of nickel titanium, one located in the top half of the wing and one in the bottom half. They then used electrical current to heat the springs, which moved the wing’s flap into the desired position. The university has filed a patent application on their invention.
“If you heat the top spring, it will basically contract and pull the flap up,” said Parsaoran Hutapea, assistant professor of mechanical engineering and the students’ faculty advisor. “Conversely, if you heat the spring on the bottom, that will contract and pull the flap down. So it eliminated the need for a hydraulic and motor system within the aircraft’s wing, because the current would be provided by a power supply already located within the aircraft.”
According to the students, the “smart wing” also offers greater fuel efficiency, lower maintenance and lower costs.
“One of the greatest advantages of using shape memory actuation to control an aircraft’s flaps would be the lightweight design that would effectually allow for greater fuel efficiency. A successfully designed shape memory alloy flap actuation system would also require low maintenance if implemented due to the small number of moving parts, and the system could be installed at relatively low cost,” they wrote in their project summary.
Hutapea said a new group mechanical engineering seniors is now working on implementing this “smart materials” concept to other navigational and steering systems throughout the aircraft as part of their senior design project.
Source: Temple University