Giving freight rail tracks a boost

The big chunks of rock—crushed limestone or dolomite that engineers call ballast—that keep railroad tracks in place look like a solid footing even as freight cars rumble overhead.
But temperature and vibration can destabilize ballast over time, keeping it from safely transferring the weight of a loaded train to the soil below, draining water and preventing vegetation from crowding the tracks.
In Wisconsin, a booming industry mining sand used by oil and gas drillers in hydraulic fracturing has presented a new challenge: fine grains of sand can leak from rail cars, accumulate in rail bed ballast and, during a rainstorm, turn into mushy, track-loosening mud.
"Some of these tracks have deteriorated so much that the trains travel at about 10 mph," says Dante Fratta, professor of civil and environmental engineering and geological engineering at the University of Wisconsin-Madison. "You have to lift up the track, remove the ballast, and put in new material. It's very expensive. It's also very expensive to have derailments."
Fratta will spend part of the spring examining these problems along a section of freight track in northern Illinois with colleagues Tuncer Edil, emeritus professor of geological engineering and civil and environmental engineering, and Jim Tinjum, professor of geological engineering.
While frac sand poses a relatively new challenge in the Midwest, the three researchers hope to bolster the nation's freight rail network against all manner of stresses that cause this particular problem, known as ballast fouling.
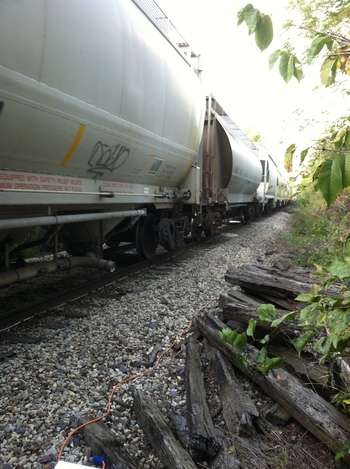
Fratta plans to install fiber optic cable in a section of track to monitor temperature, deformation and vibration in the ballast, as well as any corresponding deformation in the tracks themselves. Damage and deformation often occur within a small area of the rail bed. Fratta wants operators to have a better handle on how problems arise, giving them a better idea of how to target repairs to rail infrastructure in more cost-effective ways.
Edil is partnering with the soil stabilization and pavement lifting company Uretek to devise a system to inject polyurethane to shore up damaged or potentially weak sections of ballast. Unlike cement, liquid polyurethane is great at seeping into the voids between rocks. And while cement can take weeks or even months to set properly, polyurethane injections can set within 15 minutes.
The group still has to make sure polyurethane injection is the most cost-effective and energy-efficient approach.
"This has to beat the standard way of fixing the problem," Edil says.
Producing less replacement ballast would mean using fewer fossil fuel resources, but making polyurethane also uses energy, so Edil and Uretek have conducted a life cycle analysis to determine whether, in the long run, their process actually reduces greenhouse gas emissions and energy consumption.
Tinjum is coordinating the academic and industry teams involved, ensuring that researchers have crucial access to railroad infrastructure. For obvious reasons, railroad companies don't let just anyone experiment on their tracks, so building relationships and delivering results are important on a project like this.
"Whenever you do something for the first time, you want it to work, because you need that experience and that trust for future development," Tinjum says.
If the engineers' pilot projects pay dividends on the tracks that carry freight out of Wisconsin, the group would like to apply its concepts to other vulnerable points in railway infrastructure.
Railroad tracks take a beating at bridge approaches—where the weight of a train is transferred between surfaces with differing physical properties—and at intersections with roads, where tracks deal with the stress of trains and the weight of other vehicles.
Since injection tools have been previously used to level runways and sidewalks, Tinjum thinks they can translate well into railways.
"The immediate huge application is the remediation or improvement of the capacity of these intersections for them to last longer," he says.
Provided by University of Wisconsin-Madison