New process to prevent cold cracking in high-strength steel
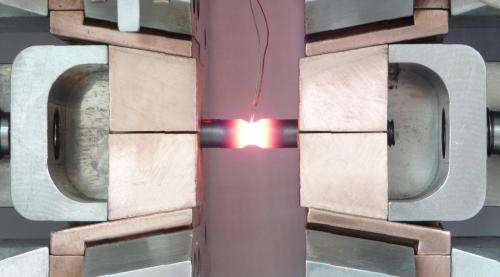
Cold cracking in high-strength steel presents major quality assurance challenges for the automotive and machine-building industries, since cracks are difficult to predict – until now. A new process can determine, as early as the design stage, if critical conditions for such damage can be prevented. This lowers development times and costs.
Cars, roof structures and bridges should become increasingly lighter, with the same stability, and thus save energy and materials. New high-strength steel is superbly suited for the needed lightweight design, because it can also withstand extremely heavy stresses. Yet these materials also betray a disadvantage: with increasing strength their susceptibility to cold cracking rises when welded. These miniscule fractures might form as the welded joints cool off – typically at temperatures below 200°C. In a worst case scenario, the welding seams would crack. For this reason, many industrial sectors are reluctant to employ these promising high-strength steel.
Scientists at the Fraunhofer Institute for Mechanics of Materials IWM in Freiburg, in conjunction with the Chair of Joining and Welding Technology LFT at Brandenburg University of Technology Cottbus (BTU) developed a new process for making cold cracking more predictable. "We are able to compute the probability of cold cracking as early as the design stage of a component, and immediately run through corrective measures as well," explains Frank Schweizer of the IWM. Because whether such cold cracking occurs, and how quickly, depends on how high the concentration of hydrogen in the steel is, how the residual stress turns out, and how its microstructure is configured. Predicting the probability of cracking has been difficult until now. Manufacturers used to conduct expensive testing, for example by applying an increasingly higher tensile stress to a sample component, and then analyse what stress level would cause cracking. Not only are these tests time-consuming and cost-intensive, the findings can-
not be applied to subsequent components on a one-to-one basis – because the geometry of the component has a decisive influence on crack formation. Even currently available computer simulations failed to deliver the desired predictive accuracy for real components.
Lowering production costs, shortening development phases
The new approach could markedly reduce such costly methods in the future – and thus lower production costs while shortening development phases. The experts at LFT set up a special test, in order to precisely determine the cracking criterion on samples of highstrength steel. Beside typical influencing factors like hydrogen content, residual stresses and material structures that can be adjusted in at the same time, they also take into account the temperature gradients that emerge in the welding process.
The experts at IWM feed a computer simulation with this criterion in order to analyze the threat of cold cracking in random components and geometries. "This way, we can locate the areas on a welding seam at risk of cold cracking, for each point and at any time in the simulated welding process," explains Frank Schweizer. The researchers can also get a preliminary look at the effects of any countermeasures, and make the necessary adjustments. To do so, they transfert the results back into the simulation, in order to fine-tune them there.
In the future, with the aid of this process, manufacturers of vehicles and machines could be able to define non-critical welding parameters and limiting conditions for their materials in advance – and thus establish a substantially more efficient and safer production process. This is especially relevant to materials that are difficult to weld, with very narrow processing windows regarding welding parameters or the pre- and post-heating temperatures. Fraunhofer IWM and LFT, in cooperation with Robert Bosch GmbH and ThyssenKrupp Steel Europe AG, are currently testing their new process on laser beam-welded demonstration models made of high-strength steels.
Provided by Fraunhofer-Gesellschaft