Time recording up one's sleeve
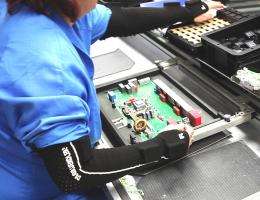
Optimized operations are essential to globally competitive companies. Until now, inspectors have timed procedures, usually manually, in order to organize manual assembly operations efficiently – a method prone to error. A new system records times automatically and cuts costs for companies.
Handling tools, assembling , inserting, joining and bolting parts, painting components, operating equipment – innumerable procedures must be executed before a product can be packaged and shipped. How much time do employees need for individual procedures? How long does manual assembly take? Industrial manufacturers have to analyze and optimize their employees’ operations continually in order to remain competitive. They must record the times of operations if they wish to analyze the individual procedures. This enables them to identify long handling distances, impractically located components, overly frequent tool changes or irregular and superfluous movements, which waste time and make production processes inefficient.
Until now, every individual movement has usually been timed by someone with a stopwatch or with digital time boards manned by employees. This approach is not really objective, however. It is replete with errors and disadvantageous for everyone involved: The stress factor for employees is extremely high and they might not execute their jobs at their usual speed. For companies, this requires quite a lot of work from staff and thus incurs high costs. There is therefore great need for more precise, automated and cost effective solutions. Contracted by the engineering firm DR. GRUENDLER in Magdeburg, researchers at the Fraunhofer Institute for Factory Operation and Automation IFF have developed such a system.
Three matchbox-sized sensors integrated in a sleeve record hand and arm movements precisely and measure the start and end of individual actions, e.g. reaching, grasping, setting up, joining, checking or releasing. The interlinked sensor modules are positioned on the upper and lower arm and the hand. Employees merely have to put on the two sleeves. They are snug like a second skin yet comfortable and do not impede the wearer. “The present stopwatch method only allows a process organizer to time five individuals simultaneously, depending on the situation. Our solution makes it possible to record time simultaneously, even at several workplaces, without requiring additional labor. The system’s greater precision and objectivity is crucial,” says Martin Woitag, research manager at the Fraunhofer IFF. Woitag and his team relied on inertial sensors for their solution. They measure the acceleration and angular velocities of arms and hands in the X, Y and Z axes. Unlike other motion tracking systems, such as GPS, the inertial measurement system functions without any other infrastructure. The inertial sensors independently detect objects’ positions in space. “What is more, our solution doesn’t require complex calibration. A tool that teaches in the measuring points directly at the assembly workplace one time is all that is needed,” according to Woitag. A PC application completes the system. The software calculates and reconstructs the motion sequences based on the sensor data. It breaks processes down into motion segments and ascertains the related times.
At present, the sleeves can be used for assembly jobs at sitting workplaces in logistics and manufacturing. In the next stage, the researchers in Magdeburg intend to configure the system to also analyze assembly operations during which workers stand or move around. They additionally plan to use the sensors to detect posture and thus analyze workplace ergonomics.
Provided by Fraunhofer-Gesellschaft