May 24, 2007 feature
Superconducting motor to increase power density
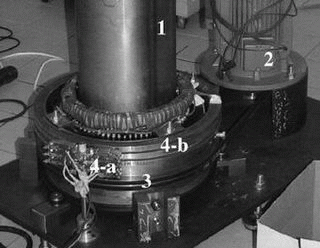
The field of electric motors has recently entered a new era. The electric motors that you see today in everything from washing machines, toys, and fans use the same basic principles as motors from 50 years ago. But with the realization of using superconducting wire to replace conventional copper coils, motors are becoming more compact, more energy efficient, and less expensive, which will have advantages particularly for large industrial applications.
Recently, scientists El Hadj Ailam and colleagues working at the Université Henri Poincaré in Nancy, France and the Center for Advanced Power Systems in Tallahassee, Florida, have designed and tested a superconducting rotating machine based on an unconventional topology. Their results, which are published in IEEE Transactions on Applied Superconductivity, show promising opportunities for the motor.
“This work has two goals,” Ailam, who is currently with the Centre Universitaire Khemis Miliana in Algeria, told PhysOrg.com. “The first is to show the feasibility of an electrical motor based on the magnetic flux density, and the second is to demonstrate that superconductors can significantly ameliorate the electrical machine performances.”
Building on high-temperature motors designed over the past few years, Ailam et al.’s motor is a low-temperature, eight-pole machine with a stationary superconducting inductor. Unlike copper coils, the niobium-titanium (NbTi) inductor coils in this design have no electrical resistance, which is one of the greatest advantages of superconductors.
When the two NbTi coils are fed with currents moving in opposite directions, the currents create a magnetic field. Located between the two coils, four superconducting bulk plates (made of YBaCuO, or yttrium barium copper oxide) shape and distribute the magnetic flux lines, which then induces an alternating electromagnetic field based on the magnetic concentration. A rotating armature wound with copper wires then converts the electrical energy to mechanical energy, which is eventually transferred to an application.
In this design, the entire inductor is cooled to 4.2 K using liquid helium to enable zero electrical resistance in the coils. (The scientists explain that high-temperature wires could also work in this configuration.) As with all superconducting motors, the superconducting wire can carry larger amounts of current than copper wire, and therefore create more powerful magnetic fields in a smaller amount of space than conventional motors.
“For the majority of electrical superconducting machines, the structure is a classical one, and the magnetic flux is a radial one,” Ailam explained. “[However,] for our machine, the inductor magnetic flux is an axial one.”
To test the performance of the motor, the scientists calculated the magnetic scalar potential, which tells the strength of a magnetic field in a certain area, and then determined the magnetic flux density, which is the quantity of magnetism in that area. As the scientists explained, the maximal value of the flux density exists in between two of the bulk plates, while the minimum value exists behind the plates; a large difference in magnetic flux density maximizes the motor’s performance by generating a more powerful magnetic field.
The group experimentally demonstrated a performance of 118.8 volts for the motor. Further, they calculated a theoretical generated voltage of 172.5 volts, and explained that the difference is due to an uncertain value for the difference in the maximal and minimal values of the magnetic fields around the bulk plates, which was not directly measured. Improving this difference in magnetic flux density will hopefully increase the motor’s voltage.
“As we demonstrate in another paper, under realization, using this structure with several superconducting wires and 20 mW generated power decreases the inductor volume 20-50 percent in comparison to a classical electrical machine,” Ailam said.
In the near future, the group plans to design and construct a 100 kW superconducting machine using the same configuration.
“The major advantages of these motors are a high power-volume density and a high torque-volume density, and less vibration than for the conventional motors,” Ailam said. “I think that the maritime propulsion can and the electrical traction generally can benefit principally to these motors.”
Citation: Ailam, El Hadj, Netter, Denis, Lévêque, Jean, Douine, Bruno, Masson, Philippe J., and Rezzoug, Abderrezak. “Design and Testing of a Superconducting Rotating Machine.” IEEE Transactions on Applied Superconductivity, Vol. 17, No. 1, March 2007.
Copyright 2007 PhysOrg.com.
All rights reserved. This material may not be published, broadcast, rewritten or redistributed in whole or part without the express written permission of PhysOrg.com.