3D laser structuring
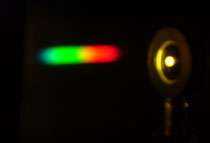
Small structure, big impact. Micrometer-fine patterns in surfaces endow components with amazing properties: Plastic dashboards, for example, can be made to look like leather; sharkskin ribs on an aircraft’s fuselage reduce air resistance; micro-recesses in implants improve connection with the bone.
There are many reasons for applying microstructures to workpieces, but actually doing so is by no means easy. While lasers have been used for quite a long time to structure flat surfaces, etching techniques have had to be deployed on three-dimensional components of complex shape - and this involves using large quantities of chemicals.
The research engineers at the Fraunhofer Institute for Production Technology IPT in Aachen have now rendered the laser fit for the third dimension. In the joint “FlexOStruk” project with nine industrial partners, they have developed a machine for near-net-shape laser ablation. This can burn microstructures into free form surfaces. The engineers are presenting the new technology on the Fraunhofer stand (Hall B3, Stand 131). A finished automobile cockpit in luxurious leather-look will demonstrate its potential.
What looks simple today is the result of months of painstaking development work. The laser has to be exactly focused so that the focal point, which is about 10 micrometers wide, works with absolute precision. It is crucial for the laser to hit the surface vertically - otherwise the focus becomes distorted and the sharp microstructure blurs. The challenge was to guide the laser precisely and always at the same distance along the curves. For this purpose the research engineers utilized the attributes of a conventional machine tool. They dismantled the tool spindle - the gripper which normally holds the milling heads - and equipped the machine with a nanosecond laser instead. A scanner controls the precise movement of the laser and lays down the desired pattern on the component. “We have ultimately succeeded in integrating the entire process from the pattern development through to the finished component in our concept,” explains Sascha Bausch, group manager for laser material processing at the IPT.
It is difficult to transfer a pattern to uneven surfaces - as anyone who has tried to wallpaper a curved surface will verify. The Fraunhofer research engineers use special CAD systems to adapt the desired structure to uneven features. The “NCProfiler” software system developed in-house converts the data provided by the scientists into control commands for the laser, the scanner and the machine tool. Working in cooperation with BMW and Siemens, the IPT engineers have already developed initial female tools for plastic injection molding and produced them using this technique. They have thus demonstrated that molds for making leather-look automobile cockpits or attractive mobile phone housings can be structured by this method.
The research engineers are currently working with a nanosecond laser, says Bausch. “Its accuracy is completely adequate for injection molding. What’s more, the laser is so energy-rich that it can achieve relatively high metal-removal rates and thus shorten production times.” This is a decisive factor for the cost efficiency of the process. The engineers intend to achieve even higher precision and even finer structures in future - for optical systems or medical technology, for instance. A further aim is to develop a series-producible machine tool for everyday industrial use.
Source: Fraunhofer-Gesellschaft