Device burns fuel with almost zero emissions
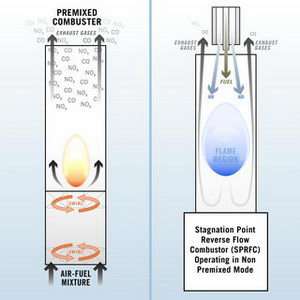
Georgia Tech researchers have created a new combustor (combustion chamber where fuel is burned to power an engine or gas turbine) designed to burn fuel in a wide range of devices - with next to no emission of nitrogen oxide (NOx) and carbon monoxide (CO), two of the primary causes of air pollution.
The device has a simpler design than existing state-of-the-art combustors and could be manufactured and maintained at a much lower cost, making it more affordable in everything from jet engines and power plants to home water heaters.
"We must burn fuel to power aircrafts and generate electricity for our homes. The combustion community is working very hard to find ways to burn the fuel completely and derive all of its energy while minimizing emissions," said Dr. Ben Zinn, Regents' professor, the David S. Lewis Jr. Chair in Georgia Tech's Guggenheim School of Aerospace Engineering and a key collaborator on the project. "Our combustor has an unbelievably simple design, and it would be inexpensive to make and inexpensive to maintain."
Attaining ultra low emissions has become a top priority for combustion researchers as federal and state restrictions on pollution continuously reduce the allowable levels of NOx and CO produced by engines, power plants and industrial processes.
Called the Stagnation Point Reverse Flow Combustor, the Georgia Tech device significantly reduces NOx and CO emissions in a variety of aircraft engines and gas turbines that burn gaseous or liquid fuels. It burns fuel with NOx emissions below 1 parts per million (ppm) and CO emissions lower than 10 ppm, significantly lower than emissions produced by other combustors.
The project's initial goal was to develop a low emissions combustor for aircraft engines and power-generating gas turbines that must stably burn large amounts of fuel in a small volume over a wide range of power settings (or fuel flow rates). But the design can be adapted for use in a variety of applications, including something as large as a power generating gas turbine or as small as a water heater in a home.
"We wanted to have all the clean-burning advantages of a low temperature combustion process while burning a large amount of fuel in a small volume," Zinn said.
The combustor burns fuel in low temperature reactions that occur over a large portion of the combustor. By eliminating all high temperature pockets through better control of the flow of the reactants and combustion products within the combustor, the device produces far lower levels of NOx and CO and avoids acoustic instabilities that are problematic in current low emissions combustors.
To reduce emissions in existing combustors, fuel is premixed with a large amount of swirling air flow prior to injection into the combustor. This requires complex and expensive designs, and the combustion process often excites instabilities that damage the system.
But Georgia Tech's design eliminates the complexity associated with premixing the fuel and air by injecting the fuel and air separately into the combustor while its shape forces them to mix with one another and with combustion products before ignition occurs.
Source: Georgia Institute of Technology