Students design 'nested' dumpster to slash shipping costs
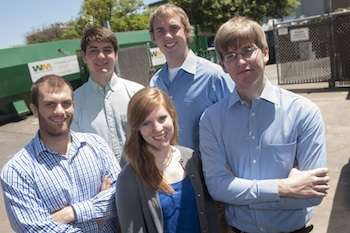
(Phys.org) —Behind strip malls and fast-food restaurants, they stand solid, dependable and mostly forgotten, awaiting our refuse.
Mobile waste receptacles, known generically as dumpsters, are as much a part of the American landscape as sidewalks and sewers. Most of the commercial waste produced in the United States ends up in them, and dumpsters have proven an efficient means of trash disposal and collection.
"The problem comes with the shipping. You can only arrange them end to end, horizontally, which means you're shipping a lot of empty space. It's not efficient and it's very expensive," said Katie Specht, a member of the design team, Container Crew, at Rice University.
When shipped from Asia, where most dumpsters are manufactured, they consume enormous amounts of empty, unutilized space—about eight cubic yards each, plus the unused space above the row of containers, meaning roughly 30 percent of the volume inside the shipping container goes unused. Because of their box-like shape, the bins can only be arranged in a row at a rate of eight per shipping container.
Specht and her teammates James Chapman, Joseph Huseman, Albert Riedel and Austin Simpson, all seniors in mechanical engineering, were assigned by Waste Management Inc., which owns the largest trucking fleet in the waste industry, to come up with a new, more-efficient design for the company's trash bins. At the start of their research last fall, each team member took an early morning ride around Houston with a Waste Management driver, observing the bins in action.
Container Crew's initial problem was a matter of pure geometry: how to "nest" the bins, reshape them so they might be transported one within another without losing volume. Last year, a different design team working in Rice's Oshman Engineering Design Kitchen, Team Breakaway Bin, had altered the design enough to increase the number that would fit into a shipping container to 24.
"That was three times as many—not bad. But we were pretty sure we could do better," Riedel said.
Huseman and Simpson handled the computer modeling for the team. After much trial and error, they ended up moving the bin's vertical lines about five degrees. This seemingly small change, coupled with the decision to make the "sleeves" (steel pieces on the sides of the bins enabling trucks to lift them) removable, made the bins "nest-able." They also proposed substituting injection-molded plastic for the conventional steel plate, but retaining a steel guard on one end of the bin to protect it from damage by garbage trucks during dumping.
As the design now stands, each bin weighs in at about 1,000 pounds, compared with 1,100 pounds for the traditional steel models. The new design will permit the transport of 42 bins per shipping container—more than five times the current number. Each must be able to withstand a load of trash weighing 4,000 pounds.
"It seems like a little thing, just changing the angle. But remember that thousands and thousands of these things are made every year. It's enormous," Riedel said.
Provided by Rice University