Detecting defects with wind and water
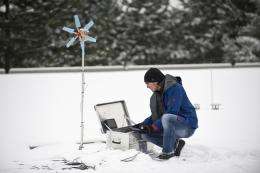
(PhysOrg.com) -- Bridges, aircraft and wind turbines are in constant movement. Natural forces and pedestrians all create vibrations. Previously, time-consuming tests were needed to determine how building components would react to vibrations. Now, researchers have developed a simpler method.
A narrow iron bridge is perched high above the river. A pedestrian on it can feel quite clearly how it vibrates the moment another person sets foot on the bridge or rides onto it on a bicycle. To ensure that people can cross the bridge in safety, time-consuming methods are employed to determine what condition the structure is in and whether it is liable to collapse.
"The vibration response of bridges is often tested using gigantic drop hammers," says Dr. Dirk Mayer of the Fraunhofer Institute for Structural Durability and System Reliability LBF in Darmstadt. Dirk Mayer and his team are currently investigating means of employing natural phenomena such as wind and water to carry out an automatic analysis of a structure's vibrational behavior. Thanks to Output Only Modal Analysis, time-consuming and expensive tests with drop hammers could soon be a thing of the past.
"Continuous vibration monitoring is important not only for bridges, but also for ships, wind turbines or airplanes," explains the Fraunhofer expert. "In the case of aircraft, electrodynamic shakers integrated under the wing surfaces are used to detect defects."
In contrast to conventional testing methods, the scientists are using neither hammers nor shakers - instead, their only tools are environmental impacts. In order to deploy the wind's capacity to cause vibrations, the experts attached two acceleration sensors to a model wind turbine. Two computers were used to process the data measured.
"It was necessary to have two because of the huge amount of data that quickly accumulates at sampling rates as low as 100 per second," explains Dirk Mayer. "While one computer preprocesses the signals and compresses the data, the second carries out another evaluation and determines the resonant frequency. If the frequency diminishes over time, it means that the stiffness of the structure is decreasing. Testers know what the rigidity or damping readings signify for their particular components or machines. "In our test we can determine whether the support of the model wind turbine is defective. In the case of bridges this method makes it possible to determine the condition of structural components by evaluating the vibrations caused by pedestrians over a period of several weeks."
Going forward, the researchers would like to offer this procedure as a service. They are also considering how unwanted vibrations could be actively dampened. The Fraunhofer experts will be presenting this new method of analysis using a model aircraft at the joint Adaptronics stand at the Hannover Messe (Germany). The eventual aim is to monitor airliners during operation.
Provided by Fraunhofer-Gesellschaft