New Process Creates 3-D Nanostructures with Magnetic Materials
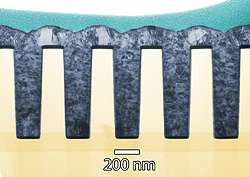
Materials scientists at the National Institute of Standards and Technology (NIST) have developed a process to build complex, three-dimensional nanoscale structures of magnetic materials such as nickel or nickel-iron alloys using techniques compatible with standard semiconductor manufacturing. The process could enable whole new classes of sensors and microelectromechanical (MEMS) devices.
The NIST team also demonstrated that key process variables are linked to relatively quick and inexpensive electrochemical measurements, pointing the way to a fast and efficient way to optimize the process for new materials.
The NIST process is a variation of a technique called “Damascene metallization” that often is used to create complicated three-dimensional copper interconnections, the “wiring” that links circuit elements across multiple layers in advanced, large-scale integrated circuits. Named after the ancient art of creating designs with metal-in-metal inlays, the process involves etching complex patterns of horizontal trenches and vertical “vias” in the surface of the wafer and then uses an electroplating process to fill them with copper. The high aspect ratio features may range from tens of nanometers to hundreds of microns in width. Once filled, the surface of the disk is ground and polished down to remove the excess copper, leaving behind the trench and via pattern.
The big trick in Damascene metallization is ensuring that the deposited metal completely fills in the deep, narrow trenches without leaving voids. This can be done by adding a chemical to the electrodeposition solution to prevent the metal from building up too quickly on the sides of the trenches and by careful control of the deposition process, but both the chemistry and the process variables turn out to be significantly different for active ferromagnetic materials than for passive materials like copper. In addition to devising a working combination of electrolytes and additives to do Damascene metallization with nickel and a nickel-iron alloy, the NIST team demonstrated straightforward measurements for identifying and optimizing the feature-filling process thereby providing an efficient path for the creation of quality nanoscale ferromagnet structures.
The new process makes it feasible to create complex three-dimensional MEMS devices such as inductors and actuators that combine magnetic alloys with non-magnetic metallizations such as copper interconnects using existing production systems.
Source: NIST