New 3-D Printer Churns Out Complex Prototypes
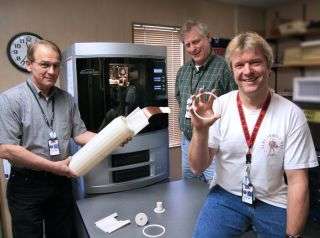
To show colleagues how a design for an accelerator component works, designer Gene Anzalone can now carry a lightweight plastic model to meetings. More tangible than a set of design drawings, and more totable than a 35-pound metal model, the working 3-D plastic model of a collimator took about five days to make with SLAC Mechanical Design Department's new rapid prototyping machine, also called a 3-D printer.
Since the Dimension Elite printer arrived in early January, its tea-box-sized printing head has been on the move day and night, whirring and clicking like a home inkjet printer while it automatically builds up models by depositing thin layers of melted plastic, layer by layer. Once engineer Kurt Vaillancourt sets up the printer, which takes very little time, he lets it work unattended, saving money on machinist costs and material costs.
"It's a service for engineers and designers across the lab to study the form, fit and function of their design before cutting them in metal," Vaillancourt said.
The SLAC arm of the Large Hadron Collider (LHC) Accelerator Research Program has eagerly taken advantage of the printer—which looks like a snack vending machine—to build models of a rotatable collimator that could be part of the upgrades to the LHC. Collimators block stray particles inside a beam pipe.
"The model is accurate enough to gain an understanding of how well the parts fit together into a working assemblage, and it gives us tangible results at an early phase of the project," said engineer Steve Lundgren.
The group can test and refine its designs before sending them to the Machine Shop to build parts from quality, expensive metals.
Anzalone and Lundgren electronically sent their CAD (computer-aided design) data to the printer. Several days later, they sandwiched ball bearings between two printer-made plastic rings, and screwed the rings together to form a functional bearing at the end of the prototype collimator. Very quickly, they determined that this design for the ball bearing race worked well. Eventually, when the LHC beam accidentally strikes and damages the collimator, operators will simply rotate it to present a fresh piece of metal without interrupting collider operations.
The printer is available for SLAC use, and can support pieces up to 8 inches square by 12 inches high, in layers as thin as 0.007 inches. Pieces can be glued together, and several parts can be fabricated in one run. The printer can also automatically enlarge or reduce parts.
Source: by Heather Rock Woods, SLAC