Learning from robots
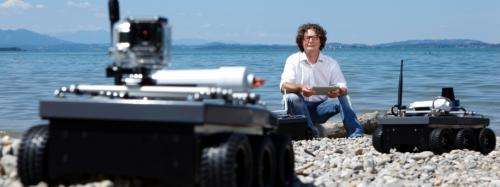
In a Bavarian village, Mathias Hubrich is building remotely controlled robots designed to perform tasks too dangerous for human beings. Robots are now also being used as teaching aids because their Siemens control systems make them ideal for learning about automation technology.
The adage about not judging a book by its cover couldn't be more appropriate in the southern Bavarian town of Chieming-Hart. The village, with its 4715 inhabitants has a church, a pub, rows of neat houses, and a small warehouse with a loading ramp and offices housed in a former bank building. But this is neither a warehouse, nor a bank, nor anything else one would expect in this picturesque retreat. For this place, in its breathtaking unobtrusiveness, is a robot factory.
Outside the building, on a quiet street where cars are rarely seen, Mathias Hubrich, the founder of robot production firm Roboterwerk GmbH, is hard at work on a summer morning at a makeshift desk. He's working here undisturbed at his Mac. The village is home to Hubrich and his company's two engineers, Arno Klüglein and Manuel Wentenschuh, who are inside the building, tightening screws and soldering components. "Many people are moving from Munich to the country," says Hubrich, who is delighted that the area has no shortage of skilled workers.
He picks up his iPhone and swipes his thumb across the display. A six-wheeled vehicle immediately begins to move. It looks a bit like an early Mars rover, but lacks the space probe's elaborate superstructure. It was in fact the Sojourner rover, which landed on Mars in 1997, that stimulated Hubrich to get into the business of building robots. Controlling robots is much easier on earth, of course. It takes signals about seven minutes to reach the Red Planet, but the small vehicle in front of the loading ramp responds instantly to every thumb swipe. The robot turns right and left, goes forward and backward, and rotates in place. Known as the Forbot A4 because it has the same dimensions as an A4 format sheet of paper, it instantly performs every command. The tiny vehicle can even climb a hill and has no problem traveling over tall grass.
Autonomous Bots
Hubrich's first concept robots, Robopark and Roboplay, were developed during the dot.com craze, when he was the CEO of an Internet firm. The devices were targeted at video game players who wanted to control real robots through the Internet. Hubrich also planned to use the robots at company events. However, these plans did not materialize, as potential investors declined to get involved. Instead, the systems attracted the attention of the German military, for which Roboterwerk GmbH has regularly conducted projects since 2004.
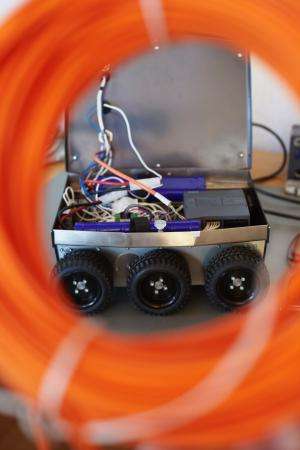
The Forbot A4 is the offspring of these early concepts; other, larger robots are taking shape in the workshop. One of them has a mount for attaching a rotating brush and a vacuum cleaner nozzle. It is designed to remove dust and grease as it travels autonomously through factory ventilation shafts. Photos taken during a test demonstrate the system's effectiveness. The ventilation shaft used for the test was dusty and encrusted, but looked like new afterwards. In Hubrich's conference room is a pushcart equipped with an electric motor at the wheels and a joystick on the handle. "We use the cart to clean paddocks," says Hubrich. To operate the system, farmers simply walk next to the pushcart, driving it along and loading it with the horse manure. "It reduces the time needed for this task by one third," says Hubrich. The part-time farming sector is expected to be one of Roboterwerk's future markets. Despite the luscious meadows, many local farmers prefer to leave their cows in the sheds because it makes farming easier. That's why the self-driving pushcarts from Chieming might also make cows happier.
Developer Arno Klüglein opens the lid of a Forbot A4. Under the WLAN antenna that links the robot to his iPhone are a sophisticated chain drive, two rechargeable battery packs, and a set of colorful wires. In the midst of it all is a small gray box bearing the Siemens logo. Most of the wires come together at this box, which is a programmable logic controller (PLC) that serves as the robot's "brain." It collects sensor signals, such as those emitted by an induction sensor, which enable the robot to follow an aluminum strip in factories, or by a laser scanner that searches the device's surroundings for obstacles. The other ends of the wires are connected to the motor. There are eight input wires and ten output wires.
The PLC must be programmed to keep the robot on track. To do this, Manuel Wentenschuh starts Siemens' TIA Portal (Totally Integrated Automation), a program that allows engineers to define the control system's behavior. Although the program has an optional window for entering cryptic programming code, most commands can be simply entered and tested with a computer mouse. The system isn't intended for lay people, but engineers only need a few hours of training before they can begin creating simple command sequences.
Usability with Totally Integrated Automation
Siemens first introduced TIA in 1996. In 2009 it added a convenient software environment, together with the new S7-1200 control system, which is also found in the A4 robot. The company merged three previously separate software modules under a uniform user interface, which it introduced as the Totally Integrated Automation Portal in 2010. The modules consist of a control configuration system, a user interface design feature and a drive parameterization function.
"The TIA Portal is a bit like Microsoft Office," says Marketing Manager Carsten Meier from Siemens. "Although programs like Word and Excel perform different tasks, they work together and are operated the same way." Moreover, the TIA Portal has a single user interface for all features; that's why it's called a portal. It was completely new at the time, and it's still unique. "None of our competitors offers anything comparable," says Meier. The introduction of the S7-1200 and S7-1500 ensured that previous S7-series control systems remained useful. Siemens has always safeguarded its customers' investments, so the TIA Portal also allows users to program older hardware.
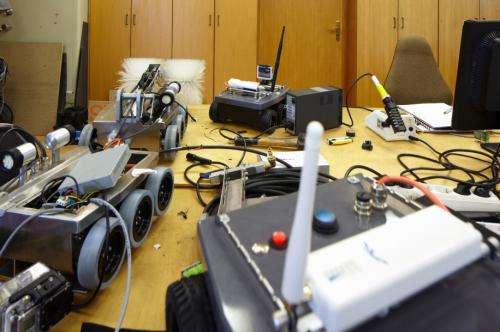
Mathias Hubrich's latest project is DRIEM2 (the German acronym for "Complete reliability for mobile manipulators"). In cooperation with the Technical University of Munich and Ingolstadt University of Applied Science, Roboterwerk is now developing a semi-autonomous robot for the German Research Ministry. The robot will be used for safety applications such as measuring pollutants. Birgit Vogel-Heuser, a professor of Automation and Information Systems at the Technical University of Munich (TUM) has the robot's predecessor in her office. The device features 1990s technology and is hard to operate. "DRIEM2 is a big improvement," she says. The original robot was used as a minesweeper. It first brought Vogel-Heuser into contact with Hubrich, through whom she got to know the big robots and small A4 models from Chieming-Hart.
Robots in the Classroom
There are two Forbot A4s in Vogel-Heuser's conference room. One of them still lacks a superstructure, but the other one is equipped with sensors and actuators that keep it from colliding with obstacles or falling off a table. However, the device can do this only if its control system is correctly programmed. This will be done by students, starting in the winter semester of 2013–14. During internships, the students will have to train the robots to fulfill certain tasks, such as traveling along a wiggly line. Although that can also be done with Lego's Mindstorms, these systems do not work with traditional control technology, says Vogel-Heuser. "Our students learn how to solve problems with industrial technology."
The students also learn how to program control systems from Siemens, the market leader. These systems are used not only in the TUM's training robots but also in over 80 percent of the machines the students will work with after they graduate. The systems are even used in beverage vending machines. The students use the TIA Portal from the start, since it has replaced older programming tools at most companies.
Most students have no problems using the Portal, says Jens Folmer, a doctoral candidate in Vogel-Heuser's department. He offers a course in the use of A4 robots in teaching. One difficulty, he says, is that programmable controls operate on the principle that real-time systems use clock cycles while sensors are queried at defined intervals. Many people are not used to this, as it contradicts the procedural programming approach used for many computer programs. "But our students quickly get the hang of it. The robots allow them to learn in a playful way," he says.
Provided by Siemens