Engineering students: Airbrush not just for artists
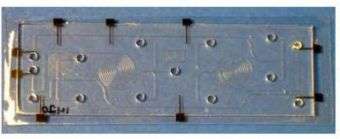
The airbrush, that tool behind tattoos and T-shirts, may have an unexpected future … in technology.
A group of engineering students at the University of Florida has come up with a method for using an airbrush to make microelectrodes — tiny conductors used in an increasing range of consumer, research and medical products. The technique is simpler than the standard one, at least for small projects that require production of only a few electrodes.
“The idea was to try to find something cheap and quick, that we could do in our own lab without much expense,” said student Corey Walker.
Walker was one of four UF engineering students who worked on the project. Now a doctoral student in biomedical engineering at the University of California, Irvine, he is the lead author of a paper appearing this month in the online edition of the journal Electroanalysis.
Microelectrodes are highly sensitive, fingernail-sized devices used, for example, in off-the-shelf glucose monitors for diabetics. They are also vital to “lab on a chip” devices under development to identify substances in air, blood or other samples.
The industry standard for manufacturing microelectrodes is screen printing, a technique that, oddly, is also borrowed from the visual arts. But it requires a screen printer, and the students, who were trying to craft a hydrogen sensor, didn’t have one.
So a student who used airbrushes to build model airplanes suggested they try that tool. Trials and tests perfected the approach, with the students eventually using fully airbrushed electrodes to craft a working sensor. The technique works best for small projects because it requires each electrode to be made individually or in small batches.
“A screen-printing machine useful for fabricating microelectrodes might cost $10,000, whereas you can buy an airbrush for less than $200,” said Hugh Fan, an associate professor of mechanical and aerospace engineering who oversaw the project. “So this is a useful technique for small, custom projects.”
Source: University of Florida