A magnetic method for polishing metals enables mold templates with microscale features
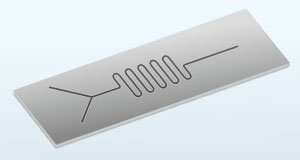
Injection molding enables large-scale production of polymer and plastic materials with micrometer-sized features. Now, A*STAR scientists have developed a method for creating mold templates with high precision and few defects.
A fluid behaves very differently when it is confined to micrometer-scale channels. This phenomenon already has several applications such as enabling the analysis of small samples of blood.
These microfluidic systems are small and portable, easy to use without expert knowledge, and disposable because they are cheap to produce. But this disposability means that microfluidic chips need to be quickly mass produced.
Now, Jiang Guo and his colleagues from the A*STAR Singapore Institute of Manufacturing Technology have developed a method for fabricating molds that can quickly create microfluidic channels in polymer substrates. "The technology addresses a critical problem in mold insert fabrication for microfluidic chip production, and will enhance local industry," says Guo.
Injection molding involves shaping a material while in a molten state using a metal template. It is cheap, fast, and useful for creating microfluidic chips. However, engineering a mold with precise micrometer-scale features and smooth surfaces is challenging as burrs and tool marks create defects. A post-polishing process can fix some of these imperfections, but it is difficult for polishing tools to access the recessed corners of microstructured surfaces and remove unwanted material uniformly.
Guo and his colleagues started by milling their template for a microfluidic channel 100 micrometers in depth and 100 micrometers in width on a special aluminum alloy. The channel was 100 millimeters in length and included two fluid inlets, one fluid outlet and a serpentine channel as reaction chamber. They then polished this template using a method known as magnetic field-assisted finishing. Two magnetic rollers rotating in opposite directions on either side of the mold create a magnetic field. This field controlled a magnetic abrasive made of carbonyl iron powder and alumina particles bound together by oil, which removed any unwanted material and smoothed the surface.
The researchers compared their template before and after this magnetic polish. They observed that the process preserved the height of the microstructure, although the edges were more rounded after polishing. The polish reduced the roughness of the surface by a factor of four, leaving a mirror-like finish. "The next step will be to use the polished mold template for actual injection molding," says Guo.
More information: Jiang Guo et al. Magnetic field-assisted finishing of a mold insert with curved microstructures for injection molding of microfluidic chips, Tribology International (2017). DOI: 10.1016/j.triboint.2017.04.019