Team illuminates transfer of nanoscale motion through microscale machine
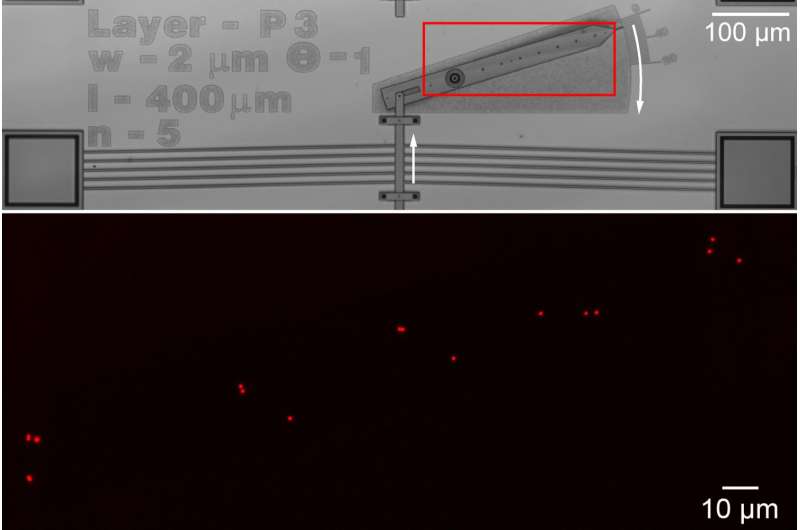
From the printing press to the jet engine, mechanical machines with moving parts have been a mainstay of technology for centuries. As U.S. industry develops smaller mechanical systems, they face bigger challenges—microscopic parts are more likely to stick together and wear out when they make contact with each other.
To help make microscopic mechanical (micromechanical) systems perform reliably for advanced technologies, researchers at the National Institute of Standards and Technology (NIST) are getting get back to basics, carefully measuring how parts move and interact.
For the first time, the NIST researchers have measured the transfer of motion through the contacting parts of a microelectromechanical system at nanometer and microradian scales. Their test system consisted of a two-part linkage, with the motion of one link driving the other. The team not only resolved the motion with record precision but also studied its performance and reliability.
Lessons learned from the study could impact the fabrication and operation of various micromechanical systems, including safety switches, robotic insects and manufacturing platforms.
The motion of micromechanical systems is sometimes too small—displacements of only a few nanometers, or one billionth of a meter, with correspondingly small rotations of a few microradians—for existing measurement methods to resolve. One microradian is the angle corresponding to the length of an arc of about 10 meters along the circumference of the earth.
"There has been a gap between fabrication technology and motion metrology—the processes exist to manufacture complex mechanical systems with microscopic parts, but the performance and reliability of these systems depends on motion that has been difficult to measure. We are closing that gap," said Samuel Stavis, a project leader at NIST.
"Despite how simple this system appears, no one had measured how it moves at the length and angle scales that we investigated," said researcher Craig Copeland of NIST and the University of Maryland. "Before commercial manufacturers can optimize the design of more complex systems such as microscopic switches or motors, it is helpful to understand how relatively simple systems operate under various conditions."
The measurements, which the researchers report in Microsystems & Nanoengineering, rely on optical microscopy to track surface features on the moving parts. The manufacturer can build in the surface features during the fabrication process so that the system is ready for measurement right out of the foundry. Or, the researchers can apply fluorescent nanoparticles to the system after fabrication for improved precision. NIST researchers introduced this measurement method in a previous study and have used related methods to track the motion and interaction of other small systems. Importantly, the ability to simultaneously track the motion of multiple parts in a micromechanical system allowed the researchers to study the details of the interaction.
In their experiment, the researchers studied the transfer of motion through a mechanical linkage, which is a system of parts connected in order to control forces and movement in machines. The test system had two links that connected and disconnected through a joint, which is the point at which the links apply forces to each other. The electrical heating and thermal expansion of one link drove the rotation of the other link around a pivot. The researchers developed a model of how the system should move under ideal operating conditions, and used that model to understand their measurements of how the system moved under practical operating conditions. The team found that play in the joint between the links, which is necessary to allow for fabrication tolerances and prevent the parts from jamming, had a central role in the motion of the system. Specifically, the amount of play was an important factor in determining precisely how the links coupled and uncoupled, and how repeatable this transfer of motion could be.
As long as the electrical input driving the system was relatively free of noise, the system worked surprisingly well, transferring the motion from one part to another very consistently for thousands of operating cycles. "It was perfectly repeatable within measurement uncertainty," said Copeland, "and reasonably consistent with our ideal model."
That is important, he notes, because some researchers expect that the friction between small parts would degrade the performance and reliability of such a system. Many engineers have even abandoned the idea of making micromechanical systems out of moving parts that make contact, switching to micromechanical systems with parts that move by flexing to avoid making contact with each other.
The results suggest that micromechanical systems that transfer motion through contacting parts "may have underexplored applications," said Stavis.
However, the researchers found that when they added a normal amount of electrical noise to the driving mechanism, the system became less reliable and did not always succeed in transferring motion from one link to the other. Further, exposure of the system to atmospheric humidity for several weeks caused the parts to stick together, although the researchers could break them loose and get them moving again.
These findings indicate that while micromechanical systems have the potential to transfer motion between contacting parts with unexpectedly precise performance, the driving signal and operating environment are critical to the reliable output of motion.
The team now plans to improve their measurements and extend their work to more complex systems with many moving parts.
"Micromechanical systems have many potential commercial applications," said Stavis. "We think that innovative measurements will help to realize that potential."
More information: C.R. Copeland, C.D. McGray, J. Geist, V.A. Aksyuk and S.M. Stavis. Transfer of motion through a microelectromechanical linkage at nanometer and microradian scales. Microsystems & Nanoengineering, 12 September 2016. DOI: 10.1038/micronano.2016.55
Provided by National Institute of Standards and Technology