More flexibility for lasers
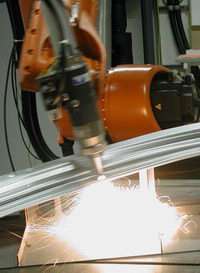
Until now, industrial lasers have been able to perform only one specific task effectively – they are generally good at either hardening, cutting or welding metal. Moreover, they are often bulky and unwieldy. Researchers from the Fraunhofer Institute for Material and Beam Technology IWS in Dresden will be presenting a real multi-talent at Laser2007 in Munich: a fiber laser system that is capable of hardening, cutting, and even welding if required.
Lasers have become an indispensable tool in many areas of industry. They are used to cut sheet metal for automobiles, harden turbine blades and weld aircraft bodies. These bundles of light energy are fast, precise, and have established a niche for themselves in many different sectors. However, despite their differences, all lasers have one thing in common: They are relatively inflexible. On the one hand, they are usually only good at performing a single task – either hardening, cutting or welding. On the other hand, many industrial lasers take the form of large, unshapely cabinets that can only work on complex three-dimensional components with a great deal of technical effort.
Researchers at the IWS have found a way of making lasers more flexible. To achieve this, they have harnessed a relatively new technology: fiber lasers. For a long time, the use of fiber lasers was confined to applications in the telecommunications sector. Their signals were just strong enough to send tiny light pulses along the glass fibers that carried telephone conversations and Internet messages. In the meantime, however, fiber lasers have caught up with their more powerful cousins. In the last few years, fiber lasers have been developed that can generate light with an output of several kilowatts in fibers with a thickness of only 50 microns.
They have the advantage that their fibers are as flexible as a cable, allowing them to get close to components with a complex geometry. Additionally, fiber lasers generate light with a wavelength of around one micron, a good wavelength for absorption by metals such as steel and aluminum. The energy of the laser easily penetrates the material to be worked. A fiber laser can therefore cut twice as quickly as a CO2 laser with the same output power and a wavelength of 10 microns, until now the laser of choice for cutting applications. Thanks to its pliable fibers, the fiber laser can be employed in a number of materials processing applications and can be easily and flexibly integrated into a production line.
The IWS researchers will be presenting fiber lasers as part of their newly developed laser cutting and hardening system at Laser2007 in Munich from June 18-21. The device is equipped with a robot arm that can skillfully guide the fiber and the laser head into even the most inaccessible corners of complex components. “Our system is particularly suitable for small and medium sized enterprises,” says Dr. Steffen Bonß, who is responsible for the laser hardening components in the system. “Because conventional laser systems usually perform only one task, smaller companies are often unwilling to invest in them.” With this new combi-system, companies are able to exploit the laser more flexibly, for either hardening or cutting depending on their current requirements. In pilot projects, the functionality of the system has been extended to include welding. This means that, for the first time, it is worthwhile even for smaller companies to invest in a laser. Without its robot arm, the fiber laser is approximately the same size as a refrigerator and thus barely half the size of a CO2 laser – another factor that facilitates flexible deployment. “A system such as ours is especially interesting for the production of prototypes or small batches,” explains Bonß.
The versatility of the system is largely due to the quality of the laser beam itself. The fibers generate very uniform light and a very small focal spot. The laser can focus the energy more effectively, operating more rapidly and with greater precision. “As far as laser cutting is concerned, CO2 lasers are the most popular with a market share of more than 90 percent,” says Dr. Thomas Himmer, project manager for laser cutting applications at the IWS. “However, they are primarily used for cutting flat sheet metal. It takes considerably more effort to utilize them for cutting more complex geometrical shapes.” This is not the case with the robot-controlled fiber laser: It can reach into any corner of a component. Additionally, thanks to improved focusing capabilities, remotely controlled processing can be carried out at higher speeds and at greater distances from the workpiece.
Moreover, the fiber laser can boast an energy conversion efficiency of 20 percent, compared to the 6 to 10 percent achieved by CO2 lasers.
Of course, there are not only CO2 and fiber lasers. The diode laser has also established a niche for itself, especially for the surface hardening of components – the sharp edges of tools, for example. It generates readily absorbable light with a short wavelength that can easily penetrate metal, as does the fiber laser. For hardening purposes, a wider focal spot is required so that a larger surface area can be processed in a short time. The narrow focus of the IWS fiber laser can be expanded and formed into the appropriate shape with the help of the LASSY beam shaping system, likewise a development of the IWS. Not only the diameter of the beam is important, but also its shape, as the corners of components can be more easily hardened with a rectangular beam than with a round beam. LASSY forms the beam into the required shape, using its integrated camera based heat sensor technology to ensure that the workpiece does not overheat.
For precision laser cutting, the focal spot should be as small as possible. While this is no problem for fiber lasers, diode lasers cannot compete in this respect. The diode laser is relatively inexpensive and still the tool of choice for laser hardening processes, but this is of little use to companies that also need to cut or weld from time to time. In future, fiber lasers will be able to perform all of these tasks. “The first fiber laser systems are already in operation in the automobile industry and are being used by both OEMs and suppliers,” explains Himmer. In collaboration with customers, he and Bonß are developing the optimum laser design: adapting beam parameters to workpieces and integrating laser systems into existing production lines. Thanks to their speed and precision, the use of lasers can often considerably shorten cycle-times, while at the same time reducing energy consumption. The researchers will be demonstrating practical examples at Laser2007 in Munich.
Source: Fraunhofer-Gesellschaft