Plastic components from the microwave
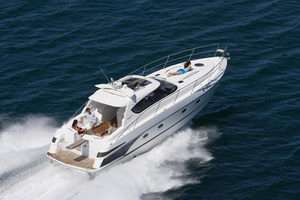
Manufacturing fiber-reinforced plastic components for ships, facades of buildings and wind power plants is a technically difficult process. Researchers are now developing a new, environment-friendly process that enables the curing process to be accurately controlled.
The shipbuilding, construction and wind power plant industries all require large components made of fiber-reinforced plastics. To produce them, the plastic is either poured into molds or applied manually layer by layer. Both methods have their pitfalls. If the casting mold is not completely filled, the component has to be discarded. The manual lamination process releases styrene, a volatile hydrocarbon that is harmful to health.
To complicate matters still further, the polyester resins mixed with the hardener and a catalyst will set at different rates depending on the ambient temperature. “The variable outside temperature during production has so far always made it impossible for us to reproduce the chemical process with any degree of accuracy,” states Dr. Rudolf Emmerich, project manager at the Fraunhofer Institute for Chemical Technology ICT in Pfinztal.
Under his leadership, a team of research institutes and companies from Germany, Slovenia and Spain is about to revolutionize the production of large-scale fiber-reinforced plastic components. The European Union is investing one million euros, or roughly 50 percent of the cost, in the research project. Its goal is to achieve improved working conditions, lower pollution and higher quality.
The polyester resin mixture will in future be of low viscosity – so liquid, that is, that it will not set at normal ambient temperatures. Using this resin, the fibers – glass fiber or foam fabric – can be embedded properly while still leaving enough time to make adjustments. Not until the constituents are correctly positioned in the mold is the component finally cured – using microwaves.
The crucial factor is “that we heat up and thus cure the components uniformly, regardless of their geometry,” says Rudolf Emmerich, explaining the challenge facing the ICT researchers. Movable antennas will transmit the microwaves and distribute the energy as required. The technical structure, the intensity of the microwave radiation and the new chemical composition of the polyester resins have already been specified. The method is now being adapted for industrial-scale applications. A prototype plant has already been completed.
Source: Fraunhofer-Gesellschaft