Researchers develop environmentally friendly coatings for military applications
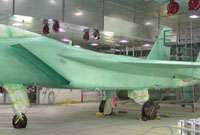
Researchers at the University of Missouri-Rolla are helping to develop a two-layer, chromate-free coating system to protect military equipment, especially aircraft, from corrosion. The two layers consist of a non-chromate conversion coating and self-priming ultra-violet light materials.
The environmentally benign conversion coatings and corrosion inhibitors would eliminate human exposure to toxic, carcinogenic chromate compounds. Also, the UV-curable layer would eliminate the use of volatile organic compounds (VOCs), which are currently released into the atmosphere during the application and curing of corrosion coatings.
An added benefit to using UV-curable materials is that it would only take seconds for the coating to cure instead of days, says Dr. Matt O’Keefe, professor of materials science and engineering at UMR.
O’Keefe and other UMR researchers are working with Boeing Corp.’s Integrated Defense Systems in St. Louis and a company called Light Curable Coatings in Cleveland to develop the new coating system for the military. The system combines rare-earth cerium oxide conversion coating processes developed at UMR with UV self-priming topcoats from Boeing and Light Curable Coatings.
The U.S. Occupational Safety and Health Administration and the Environmental Protection Agency recently decreased the acceptable exposure limit of humans to hexavalent chromium compounds. In addition, regulations on the amount of VOCs that can be released into the atmosphere restrict their use in many locations.
Due to the regulations, there is an urgent need to find replacements for chromate compounds, according to O’Keefe.
UMR previously developed chromate-free corrosion inhibitor technology through support from Boeing and the U.S. Air Force, and that technology was later licensed by Deft Industrial Finishes. Deft currently supplies the chromate-free primer that is being used to coat the Air Force’s entire F-15 fleet of aircraft.
“The new project we’re working on goes further by eliminating VOCs from the coating system and eliminating chromates from the conversion coating,” O’Keefe says.
Corrosion-related maintenance costs the U.S. Military about $20 billion annually. Chromate-based coatings are very effective at preventing the corrosion of aircraft, but they also pose a health hazard to workers applying and removing the primer and paint. Applying chromate-based coatings can cause severe respiratory problems, and in some cases may lead to lung cancer.
“The Air Force has identified the coating of aircraft as a major part of their pollution reduction and prevention program,” O’Keefe says. “They are also aware that waiting for the coatings to cure impacts force readiness. We are trying to address both of these issues by developing corrosion coatings that are environmentally friendly and get the equipment available for service in a much shortened amount of time.”
O’Keefe and Dr. Bill Fahrenholtz, an associate professor of materials science and engineering at UMR, are the lead researchers on the UMR part of the project, which focuses on the non-chromate conversion coatings. John DeAntoni of Boeing and Dr. Ben Curatolo of Light Curable Coatings are the principal investigators with respect to the UV-curable coatings.
Continuing research on environmentally friendly corrosion coatings at UMR is funded by the Strategic Environmental Research and Development Program and monitored by the Air Force Research Laboratory.
O’Keefe says he hopes the new coating system can eventually be commercialized.
Source: University of Missouri-Rolla