July 22, 2010 feature
Solar-powered process could decrease carbon dioxide to pre-industrial levels in 10 years
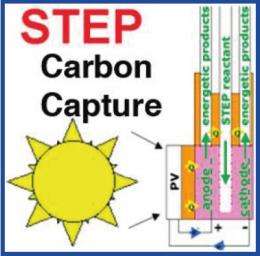
(PhysOrg.com) -- By using the sun's visible light and heat to power an electrolysis cell that captures and converts carbon dioxide from the air, a new technique could impressively clean the atmosphere and produce fuel feedstock at the same time. The key advantage of the new solar carbon capture process is that it simultaneously uses the solar visible and solar thermal components, whereas the latter is usually regarded as detrimental due to the degradation that heat causes to photovoltaic materials. However, the new method uses the sun’s heat to convert more solar energy into carbon than either photovoltaic or solar thermal processes alone.
The new process, called Solar Thermal Electrochemical Photo (STEP) carbon capture, was recently suggested theoretically by a team of scientists from George Washington University and Howard University, both in Washington, DC. Now, in a paper just published in The Journal of Physical Chemistry Letters, the scientists have experimentally demonstrated the STEP process for the first time.
“The significance of the study is twofold,” Stuart Licht, a chemistry professor at George Washington University, told PhysOrg.com. “Carbon dioxide, a non-reactive and normally difficult-to-remove compound, can be easily captured with solar energy using our new low-energy, lithium carbonate electrolysis STEP process, and with scale-up, sufficient resources exist for STEP to decrease carbon dioxide levels in the atmosphere to pre-industrial levels within 10 years.”
As the scientists explain, the process uses visible sunlight to power an electrolysis cell for splitting carbon dioxide, and also uses solar thermal energy to heat the cell in order to decrease the energy required for this conversion process. The electrolysis cell splits carbon dioxide into either solid carbon (when the reaction occurs at temperatures between 750°C and 850°C) or carbon monoxide (when the reaction occurs at temperatures above 950°C). These kinds of temperatures are much higher than those typically used for carbon-splitting electrolysis reactions (e.g., 25°C), but the advantage of reactions at higher temperatures is that they require less energy to power the reaction than at lower temperatures.
The STEP process is the first and only method that incorporates both visible and thermal energy from the sun for carbon capture. Radiation from the full solar spectrum - including heat - is not usually considered an advantage in solar technologies due to heat’s damage to photovoltaics. Even in the best solar cells, a large part of sunlight is discarded as intrinsically insufficient to drive solar cells as it is sub-bandgap, and so it is lost as waste heat.
By showing how to take advantage of both the sun’s heat and light for capturing and splitting carbon dioxide, the STEP process is fundamentally capable of converting more solar energy than either photovoltaic or solar thermal processes alone. The experiments in this study showed that the technique could capture carbon dioxide and convert it into carbon with a solar efficiency from 34% to 50%, depending on the thermal component. While carbon could be stored, the production of carbon monoxide could later be used to synthesize jet, kerosene, and diesel fuels, with the help of hydrogen generated by STEP water splitting.
“We are exploring the STEP generation of synthetic jet fuel and synthetic diesel,” Licht said, “and in addition to carbon capture, we are developing STEP processes to generate the staples predicted in our original theory, such as a variety of metals and bleach."
• Learn about becoming PhysOrg.com sponsor and ads-free website
More information: Stuart Licht, Baohui Wang, Susanta Ghosh, Hina Ayub, Dianlu Jiang, and Jason Ganley.” J. Phys. Chem. Lett. 2010. 11 2363-2368. DOI:10.1021/jz100829s
Copyright 2010 PhysOrg.com.
All rights reserved. This material may not be published, broadcast, rewritten or redistributed in whole or part without the express written permission of PhysOrg.com.