UWE researchers reinvent the potters wheel
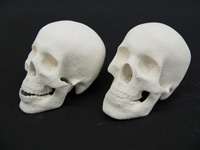
(PhysOrg.com) -- Broken the lid of your favourite ceramic teapot but can't buy a replacement? Worry not. Researchers from the Centre for Fine Print Research (CFPR) at the University of the West of England, Bristol, have discovered a new way of using 3D printing technology (rapid prototyping) which will allow an exact real clay replacement to be printed using a digital file.
This research in 3D printing technology means that a cup, a saucer, or almost any 3D shape can be rapidly built in ceramic materials from a computer generated file, and then placed in the kiln and fired. This process moves rapid prototyping from its classification as a prototyping process towards a production process.
Previous means of producing a prototype typically took many hours, tools, and skilled labour; drawings were sent to skilled craftspeople where the design on paper was painstakingly followed, and a three dimensional prototype was produced by hand. This was not a speedy process, and costs of the skilled labour were not cheap, hence the need to develop a faster and cheaper process to produce prototypes. As an answer to this need, rapid prototyping was born. For instance, if you break the heater knob in your car - at present you have to go to a retailer, who either stocks thousands of similar parts on the shelf or has to order the part from a wholesaler, which takes time, and requires huge transport and overhead costs. In future, with the aid of rapid prototyping technology, you will collect a replacement from a high street 3D copy shop, who will print you a part to order from a downloaded file.
The technology is developing fast. The Centre for Fine Print Research has taken a clear lead in the quality of objects that can be printed. The research team have developed novel ceramic materials which replace the plaster powder currently used for the rapid prototyping process. This takes rapid prototyping from the realm of being able to replicate a model of an object to being able to print the actual object digitally, to order.
Until now it has been possible to print ceramic materials in this manner, although the density and shrinkage of the objects produced did not achieve the demands of the ceramic industry. Following a three year research project, funded by the AHRC, researchers investigated how the latest technology in 3D printing could be used to create one-off functional bespoke artworks, rather than creating a prototype which forms the basis for a mould or has to be recreated in another media. This new process allows the artist to develop the object digitally on screen and then produce the finished work directly in “real” ceramic materials. The object is then placed in a kiln and fired. The technology has potential for use in the wider ceramics industry; it will now be possible, not only to make exact trial versions in ceramic before a production run, but to operate specialist short runs which allow every piece to be different. In the long term the technology may have implications in the medical field, as research is already taking place for ceramic replacements in serious bone fractures.
David Huson, who worked on developing the new ceramic method, explains, “My background is in ceramics, so when I first saw this machine I was excited by the potential to find new uses for it. During our research we tried many different methods and processes for ceramics and looked at different substances. One of the key challenges was to develop ceramic objects which were strong enough when they came out of the printer, but still had the right properties to be able to be fired in a kiln. We needed to develop something which would allow for the same density and shrinkage of traditional ceramic materials, and also meet the requirements of the ceramics industry.
“This new development could open doors for artists working in ceramics to create designs using a computer, which were not possible in the past. For example we can design an object, such as a ball inside a lattice sphere, which is impossible to create in any other method, but can now be made in a single process using the new technology.”
The team used current 3D technology (such as the Z Corp printer), which uses an inkjet printing system. In this system a bed of powder (instead of paper) is printed with a bonding liquid (instead of ink) which builds up an object in layers, working from a computer design as the print head passes back and forth over the powder. On completion the finished object is removed from the powder and cleaned.
The research team, led by Professor Steve Hoskins, includes Dave Huson, Dr Paul Thirkell and Dr Peter Walters. The team are applying for an international patent for their new method, and produced a number of research articles and conference papers reflecting on their findings which may be found on the CFPR website
“3D 2D 3D” is a unique exhibition curated by Dr Paul Thirkell, senior research fellow at CFPR, celebrating the work of artists who are using 3D print. Each artist will produce both a 2D (digital print) and a 3D printed object that in some way sets up a relationship or an interaction between the 2 dimensions to reveal insights into image and object making through print.
Provided by University of the West of England