Intelligence inside metal components
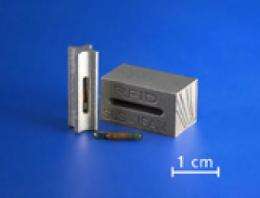
Up to now, extreme production temperatures made it impossible to equip metallic components with RFID chips during the operating process. At Euromold in Frankfurt (Dec. 2-5), Germany, Fraunhofer researchers present a variation on a process that makes the non-destructive integration of radio chips a reality.
Whether it's CD packaging, containers or identification cards: RFID tags (Radio Frequency Identification) are increasingly finding their way into everyday life. They make it possible to label objects or goods and identify them automatically by radio frequency. The appropriate scanner can read and process the data contained in the label. »Smart labels« can be affixed to goods under production conditions of up to 100 degrees Celsius. But at higher temperatures - such as with laser fusion - they fall apart: the metal components are being manufactured out of stainless steel powder, using a laser at temperatures in excess of 1400 degrees Celsius. Such production conditions precluded the use of radio-based identification - until now.
Recently, researchers from the Fraunhofer-Institute for Manufacturing and Advanced Materials IFAM in Bremen developed a new, non-destructive process. They use the »Rapid Manufacturing« method: A machine produces a component based on a three-dimensional CAD model, building it layer-by-layer directly from the computer. The laser melts off the areas of each metal powder layer that are intended to be solid. Next, the building platform is lowered and the process restarts until the component is completed. Fraunhofer scientists can control this process in a manner that allows the RFID to be installed and completely encased by the material.
»This new process finally puts the intelligence into the metal component. You can store critical information in the radio tags, like the serial number or the manufacture date. So, for example, companies now can make their top-grade replacement parts tamper-proof and resistant to fraud,« explains project manager Claus Aumund-Kopp. If someone tries to remove the chip, they will wind up destroying it in the attempt. And soon, it will be possible to do more than just reading the identification code. Conceivably, it might even be possible to store information during the period of usage. Experts also envision the potential of this process as it relates to sensors or actuators: With the aid of temperature or expansion sensors, it may be possible to record data on thermal or mechanical stresses on the components.
In addition, the new Fraunhofer Additive Manufacturing Alliance will present technologies and services along the entire value creation chain. This includes everything from additive manufacturing technologies and tools manufacturing through to tooling, repair and maintenance. Ten institutes have joined together under the aegis of the alliance.
Source: Fraunhofer-Gesellschaft (news : web)