Glass you can build with: Metallic glass that's stronger and lasts longer
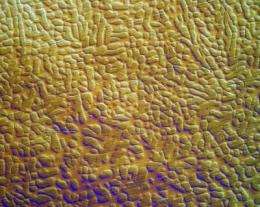
(PhysOrg.com) -- The normal structure of metals is crystalline. Glass, on the other hand, is amorphous. But it's possible to make amorphous forms of metal, metallic glasses, which can be remarkably strong, having many properties equal to or better than their crystalline metal cousins. The catch is that bulk metallic glasses are highly susceptible to fatigue, a severe problem for their use as structural materials.
Now researchers at the U.S. Department of Energy's Lawrence Berkeley National Laboratory and the University of California at Berkeley, working with colleagues at the California Institute of Technology, have solved the fundamental problem of poor fatigue resistance in bulk metallic glasses. The results are metallic glass alloys that are not only stronger than high-strength steel and aluminum alloys but more resistant to fatigue as well.
Bulk metallic glasses
For a decade or so it has been possible to make metallic glasses in bulk - just like regular crystalline metals - by using a number of tricks: rapidly cooling the liquid metal, for example, and mixing together several elements with different crystalline structures - "which because they don't know how to crystallize, delays the crystallization and allows you to create an amorphous structure," as Robert Ritchie of Berkeley Lab's Materials Sciences Division explains.
The excitement that greeted the ability to make metallic glasses in bulk has not been followed up by widespread technological use, however. These alloys were first employed for lightweight, springy gold clubs, but to date there have been few, if any, important structural applications - in the aerospace industry, for example, as was initially hoped.
"One reason for this is that properties associated with cracking or fracture - such as fracture toughness or fatigue resistance - in these bulk metallic glass have often been quite poor," says Maximilien Launey, a postdoctoral research fellow working with Ritchie at Berkeley Lab.
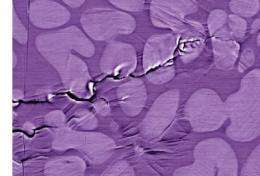
"Without good toughness, these alloys have found few applications structurally," says Ritchie, who is also a professor in UC Berkeley's Department of Materials Science and Engineering. "Moreover, their fatigue resistance is also quite poor, with fatigue limits sometimes as low as one tenth or so that of most crystalline metallic alloys."
Since fatigue is the most widespread mechanism of degradation in metallic structures, low fatigue resistance has impeded the adoption of metallic glasses as structural materials.
"While it has been often thought the fatigue limit was the cyclic stress needed to initiate a crack in a material, there are always small cracks present," Ritchie says. "The fatigue limit is actually the cyclic stress needed to get such a small crack propagating."
In crystalline materials there are many barriers to crack propagation, including grain boundaries, inclusions, and other microstructural obstacles. Says Ritchie, "The fatigue limit is the stress needed to get cracks past such barriers." But metallic glasses have no crystalline structure, so no such barriers exist.
"If a crack is present, there's nothing to stop it from propagating," says Ritchie. "In metallic glasses, dominant shear bands can form and extend throughout the material; under tensile stress, this can lead to premature catastrophic failures at very small strains -- a particular problem in metallic glasses."
Stopping runaway cracks
Ritchie and Launey worked with colleagues Douglas Hofmann and William Johnson at Caltech to find a solution. Johnson's group at Cal Tech had developed a metallic glass alloy named DH3, made from five elements - roughly a third zirconium, a third titanium, and the remainder niobium, copper, and beryllium. In bulk samples of DH3 the researchers induced a second phase of the metal, which took the form of narrow pathways of crystalline metal permeating the metallic glass in dendritic (treelike) patterns; its growth was carefully controlled by processing a partially molten liquid-solid mixture.
The resulting dendritic phase acts as a local arrest point to any crack that begins to propagate in the glass.
"The process of blocking these shear bands is important not just for fatigue but for toughness as well," Launey says. "The approach of using a second phase has been tried before, but hasn't always been very successful. What this study shows is that it is their separation that is critical; the spacing of these arrest points has to be small enough to arrest any crack before it becomes large enough to cause catastrophic failure."
The goal is to match the mechanical and microstructural scales of the material: the microstructural scale is the space of the dendritic branches, while the mechanical scale is the length of a crack that breaks the material.
"So it is important that any shear band or crack is arrested before it makes it that far," Ritchie says. "We do that by having a finer distribution of these second phases" - with dimensions determined by a simple formula - "and as a result we got far superior fatigue resistance."
So good, in fact, that toughness, ductility, and fatigue resistance - all intimately related properties - of the DH3 alloy improved to the point that the bulk metallic glass was not only stronger than many structural metal alloys but had a fatigue limit more than 30 percent higher than ultra-high-strength steel and aluminum-lithium alloys.
"The important point here is that these design strategies can be universally applied to any other metallic glass systems," Launey says. "As a result, we feel the fatigue problem in metallic glasses can be solved."
More information: "Solution to the problem of the poor cyclic fatigue resistance of bulk metallic glasses," by Maximilien E. Launey, Douglas C. Hofmann, William L. Johnson, and Robert O. Ritchie, appears in the Proceedings of the National Academy of Sciences, and is available online to subscribers in the PNAS Early Edition, 16 March 2009, at www.pnas.org/content/early/200 … /0900740106.abstract
Source: Lawrence Berkeley National Laboratory (news : web)