USC's 'print-a-house' construction technology
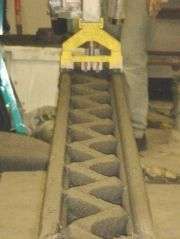
Caterpillar, the world's largest manufacturer of construction equipment, is starting to support research on the "Contour Crafting" automated construction system that its creator believes will one day be able to build full-scale houses in hours.
Behrokh Khoshnevis, a professor in the USC Viterbi School of Engineering, says the system is a scale-up of the rapid prototyping machines now widely used in industry to "print out" three-dimensional objects designed with CAD/CAM software, usually by building up successive layers of plastic.
"Instead of plastic, Contour Crafting will use concrete," said Khoshnevis. More specifically, the material is a special concrete formulation provided by USG, the multi-national construction materials company that has been contributing to Khoshnevis' research for some years as a member of an industry coalition backing the USC Center for Rapid Automated Fabrication Technologies (CRAFT), home of the initiative.
The feasibility of the Contour Crafting process has been established by a recent research effort which has resulted in automated fabrication of six-foot concrete walls.
Caterpillar will be a major contributor to upcoming work on the project, according to Everett Brandt, an engineer in Caterpillar's Technology & Solutions Division, who will work with Khoshnevis. Another Caterpillar engineer, Brian Howson, will also participate in the effort.
Goals for this phase of the project are process and material engineering research to relate various process parameters and material characteristics to the performance of the specimens to be produced. Various experimental and analytical methods will be employed in the course of the research.
Future phases of the project are expected to include geometric design issues, research in deployable robotics and material delivery methods, automated plumbing and electrical network installation, and automated inspection and quality control.
Source: University of Southern California