Soldered lenses
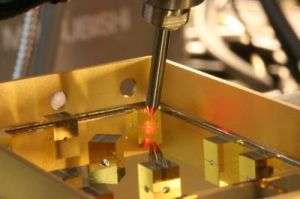
Lenses in optical devices are kept in place by adhesives. This can cause problems when the microscopes and cameras are employed inside a vacuum, as the adhesives may release gases that contaminate the lenses. One alternative is to solder them instead.
When cameras and microscopes are placed in a vacuum, their functionality can be seriously impaired. This is because their lenses and prisms are normally fixed with adhesives, which release gases inside the vacuum. The gas molecules settle on the lenses and alter their optical properties. At high temperatures, too, or when using lasers in the UV range, the adhesives cause problems: They become soft or brittle, and the optical components can slip by several micrometers.
Researchers at the Fraunhofer Institute for Applied Optics and Precision Engineering IOF in Jena have now developed an alternative in a joint project with engineers from Pac Tech GmbH in Nauen. “We solder the optical components instead of gluing them,” says IOF group manager Dr.-Ing. Erik Beckert. “This has a definite advantage: The solder material is resistant to extreme temperatures and radiation, and also conducts heat and electricity.”
To enable them to apply the solder to the lenses just as flexibly as an adhesive, the researchers adapted the ‘solder bumping’ technique normally used in electronics manufacture. Small balls of solder contained in a dosing head slip one by one into a capillary, where a laser beam heats them until they become liquid. The liquid solder droplets are then shot by a nitrogen pressure pulse to the spot where they are needed to fix the lens. Once in place, the solder cools in just a few milliseconds and solidifies.
“This process can be automated and is very flexible. We can apply the solder downwards or from various other angles and in places that are difficult to access,” says Beckert. Solder bumping is much faster than gluing. While it takes 10 to 30 seconds to apply an adhesive and let it harden, soldering takes less than one second. To ensure that the solder does not come off the glass lenses, they have to be metallized in advance, for instance in a sputtering process which can be carried out on a large scale.
A special feature of the solder bumping process is that it does not need a fluxing agent. “Normally, flux is used to ensure that the solder fully coats the metal. However, in a vacuum, the flux residues would outgas in a similar way to adhesives. The lens system would have to be thoroughly cleaned before being used. That’s not necessary with the flux-free version,” says Beckert.
At Optatec, which will take place in Frankfurt (Germany) on June 17 through 20, the researchers will present prototypes of optical components fixed in place by solder bumping. Beckert hopes that the system will be ready for use in production in a year or two’s time.
Source: Fraunhofer-Gesellschaft