Making a good impression: Nanoimprint lithography tests at NIST
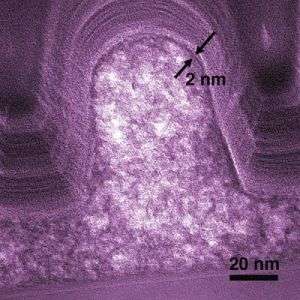
In what should be good news for integrated circuit manufacturers, recent studies by the National Institute of Standards and Technology have helped resolve two important questions about an emerging microcircuit manufacturing technology called nanoimprint lithography—yes, it can accurately stamp delicate insulating structures on advanced microchips, and, no, it doesn’t damage them, in fact it makes them better.
An emerging manufacturing technique, nanoimprint lithography (NIL) is basically an embossing process. A stamp with a nanoscale pattern in its surface is pressed into a soft film on the surface of a semiconductor wafer. The film is hardened, usually by heating or exposure to ultraviolet light, and the film retains the impressed pattern from the stamp. The process is astonishingly accurate. NIL has been used to create features as small as ten nanometers across with relatively complex shapes.
NIL is being eyed in particular for building the complexly patterned insulating layers sandwiched between layers of logic devices in future generations of integrated circuits. State-of-the-art semiconductors contain over a billion transistors, packed together into a footprint of silicon that is no bigger than a few square centimeters. Several miles of nanoscale copper wiring are required to connect the devices, and these wires must be separated by a highly efficient insulator.
One candidate is a porous glassy material called SOG* that can be applied as a thin fluid film. When heated, SOG turns into a thin glass film laced with nanometer pores that enhance the electrical insulation. But SOG is relatively delicate, and the conventional photoresist etching process used to cut trenches for the wiring can compromise it. NIL, on the other hand, might be able to pattern SOG layers with wiring trenches and eliminate several time-consuming and expensive photolithography steps if it could pattern the film accurately and do so without destroying the delicate nanopore lacework.
In a paper published last fall,** NIST materials scientists addressed the first question. Using sensitive X-ray measurements they demonstrated that NIL could be used on a functional SOG material to transfer patterns with details finer than 100 nanometers with minimal distortion due to the processing. In a new paper this month,*** they extend this work to study the effect of the embossing process on the nanopore structure in the glass. Using a combination of techniques to measure the distribution of nanopores in the insulator material, they found that the NIL embossing process actually has a beneficial effect—it increases the population of small pores, which improve performance, reduces the population of larger pores that can cause problems and creates a thin, dense protective skin across the surface of the material. All of these effects are highly attractive for minimizing short circuits in semiconductor devices.
Taken together, the two papers suggest that nanoimprint lithography can produce superior nanoporous insulator layers in advanced semiconductor devices with significantly fewer—and easier—processing steps than conventional lithography.
* “Spin-on organosilicate glass”
** H.W. Ro, R.L. Jones, H. Peng, D.R. Hines, H-J. Lee, E.K. Lin, A. Karim, D.Y. Yoon, D.W. Gidley and C.L. Soles. The direct patterning of nanoporous interlayer dielectric insulator films by nanoimprint lithography. Advanced Materials. 2007, 19, 2919–2924.
*** H.W. Ro, H. Peng, K.-i. Niihara, H.-J. Lee, E.K. Lin, A. Karim, D.W. Gidley, H. Jinnai, D.Y. Yoon and C.L. Soles. Self-sealing of nanoporous low dielectric constant patterns fabricated by nanoimprint lithography. Advanced Materials 2008, Early View: April 15, 2008.
Source: National Institute of Standards and Technology