Lego system for production facilities
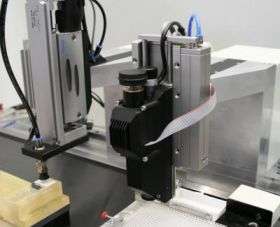
Things that work on a small scale are not necessarily as successful on a large one. It takes a lot of patience and money to scale up analytical or therapeutic processes from the laboratory to industrial manufacture. A new platform made of building blocks minimizes the cost.
Laboratory equipment for medical issues – such as blood tests – and production equipment for medical accessories have one thing in common: They are difficult to plan, as so many different components are involved. Where should which pumps and which dosing systems be located in order to produce and analyze a biochip, for example, in the best way possible?
So far, manufacturers of complex laboratory equipment have first drawn up various concepts and created engineering drawings before building the actual devices. Nevertheless, when it comes to the test, the machines often do not function as expected. The planning process starts over again – a costly business. And this is not the only problem: The designers tend to use components and technologies of which they already have some experience. However, these are not always the ones that would be best for the system.
The new ‘Modular Process Automation Laboratory m:Pal’ platform makes it possible to plan complex laboratory equipment faster and more efficiently. It comes as a construction kit in which pumps, incubators, dosing devices and camera modules can be slotted together in any way desired and tried out immediately – in much the same way as Lego bricks. The ‘m:Pal’ system was developed by research scientists at the Fraunhofer Institute for Manufacturing Engineering and Automation IPA in Stuttgart. “We have developed a kind of playground in which we can straightforwardly test all the techniques and choose the ones that are most suitable for the problem in hand. Each module is completely autonomous and can therefore be operated on its own,” explains IPA team leader Andreas Traube. “The crucial issue was the software architecture, as the required modules have to work immediately at the push of a button when you fit them together.”
The platform is intended to give manufacturers of small batches a high degree of flexibility in future. “Producers of hearing aids or other medical products that come in different versions or are constantly coming out as new models can use ‘m:Pal’ as a production tool. Up to now the whole production line had to be replaced for every new model – but with ‘m:Pal’, it is sufficient to adapt one or two modules. This makes it possible to save up to 50 percent of the costs,” says Traube. Manufacturers can also automate a smaller production line step by step, gradually acquiring new modules as the throughput increases. The researchers will be presenting ‘m:Pal’ at the MEDTEC trade fair in Stuttgart on March 11 through 13.
Source: Fraunhofer-Gesellschaft