NASA Shuttle Engine Upgrades Improve Safety and Reliability
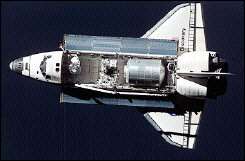
A main engine computer upgrade developed by NASA's Marshall Space Flight Center in Huntsville, Ala., will fly on space shuttle Atlantis during the STS-117 mission, targeted for launch June 8. The upgrade is part of NASA's continuing efforts to improve space shuttle safety and reliability.
The Advanced Health Management System, or AHMS, will provide new monitoring and insight into the performance of the two most critical components of the space shuttle main engine: the high-pressure fuel turbopump and the high-pressure oxidizer turbopump.
This latest improvement is to the controller, the on-engine computer that monitors and controls all main engine operations. The improvement allows an engine to shut down during launch if vibration levels exceed safe limits. AHMS consists of advanced digital signal processors, radiation-hardened memory and new software.
AHMS first flew on Discovery's STS-116 mission in December 2006 with a single controller on one engine, but in monitor-only mode, meaning AHMS collected and processed vibration data but could not shut down the engine. AHMS will operate in active mode - the ability to shut down an engine if an anomaly is detected - on a single engine during the upcoming STS-117 mission and is scheduled to fly in active mode on all three engines during the STS-118 mission later this year.
In the event of an engine shut down, the shuttle has several options available to abort the ascent. They include returning to the launch site, a transatlantic abort landing, landing at an alternate site in the United States or rendezvous with the International Space Station. Each scenario would depend on when an engine shuts down during flight, the mission trajectory and mission specific requirements, such as payloads.
The system uses data from three existing sensors, or accelerometers, mounted on each of the high pressure turbopumps. It measures how much each pump is vibrating. High-pressure fuel and high-pressure oxidizer turbopumps rotate at approximately 34,000 revolutions per minute and 23,000 revolutions per minute, respectively. To operate at such extreme speeds, the turbopumps are equipped with highly specialized bearings and precisely balanced components. Output data from the accelerometers is routed to the new digital signal processors installed in the main engine controller. These processors analyze the sensor readings 20 times each second, looking for vibration anomalies that are indicative of impending failure of rotating turbopump components such as blades, impellers, inducers and bearings. If the magnitude of any vibration anomaly exceeds safe limits, the upgraded main engine controller would shut down the unhealthy engine immediately.
"The Space Shuttle Main Engine Project has, for many years, pursued a reliable means to monitor high-pressure turbomachinery health in real time," said Tim Kelley, deputy manager of the Space Shuttle Main Engine Project Office. "AHMS provides that capability and significantly improves shuttle flight safety."
AHMS is the sixth major upgrade to space shuttle main engines since the first shuttle flight in 1981. The series of shuttle main engine enhancements have increased safety and reliability through such improvements as the addition of a two-duct powerhead, a single-coil heat exchanger, a new high-pressure oxidizer turbopump, a large-throat main combustion chamber and a new high-pressure fuel turbopump.
The shuttle's three main engines start approximately 6.5 seconds prior to lift-off. Once running, the solid rocket boosters ignite, and lift-off occurs. During ascent, the solid rocket boosters burn for approximately 120 seconds and are then jettisoned. The shuttle, still attached to the external tank with three main engines running, continues ascent until main engine cut-off at 510 seconds, or eight and one-half minutes after liftoff - long enough to burn more than 500,000 gallons of fuel. The engines shut down just before the shuttle, traveling at about 17,000 mph, reaches orbit. The three main engines are never restarted during the mission, re-entry or landing. The shuttle returns to Earth as a glider.
Space shuttle main engines operate at greater temperature extremes than any mechanical system in common use today. These powerful engines are clustered at the aft end of the shuttle and have a combined thrust of more than 1.2 million pounds. Each is 14 feet long, is seven and one-half feet in diameter at the nozzle exit, weighs approximately 7,750 pounds and generates more than 12 million horsepower.
Source: NASA