New reagents selected for nickel extraction
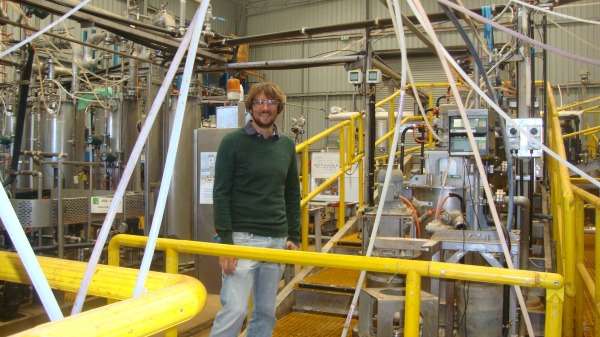
More nickel can be produced more efficiently from Australia's low-grade laterite ores if the metal is directly extracted after leaching with nitric acid, research suggests.
The extraction step, called direct solvent extraction (DSX), promises to increase the profitability of the innovative nitrate-based nickel production process pioneered by CSIRO and Direct Nickel at their Perth-based pilot plant.
Curtin University researcher Mr Mike Hutton-Ashkenny says using DSX will allow Direct Nickel to produce a purified nickel solution, rather than a nickel-rich precipitate.
"At the moment they'd sell the precipitate to a refinery, they'd just give it to someone else to deal with," he says.
"But we could use a process like DSX to selectively extract the nickel and cobalt…then purify and concentrate that out."
Mr Hutton-Ashkenny says while a commercial solution to DSX is available for conventional sulphuric acid leach solutions the use of nitric acid was unexplored territory.
"Nobody had ever tried DSX from a really concentrated nitrate solution before, nobody really knew what was going to happen," he says.
Trial and error used to find right reagent
Mr Hutton-Ashkenny's lab-based research compared the performance of three reagent (a substance used to bring about a chemical reaction) combinations in extracting nickel and cobalt from Direct Nickel's nitrate-rich leach solution.
"Inside that leach solution is nickel, cobalt, magnesium, manganese and zinc," he says.
"You don't want anything except nickel and cobalt, so you need reagents that are specific to those two, and that don't touch anything else."
While two of Mr Hutton-Ashkenny's three combinations performed well at this extraction step, only one made it through the second part of the challenge: stripping the nickel from the reagents using a commercially proven sulphuric acid wash.
"The extraction with one combination was so strong, it was actually quite difficult to get the nickel out again…it wasn't letting go of the nickel," Mr Hutton-Ashkenny says.
Mr Hutton-Ashkenny found the most promising combination—the commercially available organic acid VersaticTM10 and a pyridine carboxylate—worked with low extraction pH and low neutralisation requirements.
DSX technology could further add to the efficiencies realised by leaching ore with nitric acid instead of sulphuric acid, including lower costs, reagents recycling and reduced environmental impact: the nitrate-rich tailings can even boost plant growth by adding nitrogen to the soil.
"Using nitric acid means we can get more nickel out of the same ore body," Mr Hutton-Ashkenny says.
"Leach the nickel and cobalt out with nitric acid, use DSX to get it into sulphuric acid, and then nickel purification from there is commercially proven."
More information: "Reagent selection for recovery of nickel and cobalt from nitric acid nickel laterite leach solutions by solvent extraction," Minerals Engineering, Volume 77, June 2015, Pages 42-51, ISSN 0892-6875, dx.doi.org/10.1016/j.mineng.2015.02.010
Provided by Science Network WA