Making robotic movement of goods more 'pallet-able'
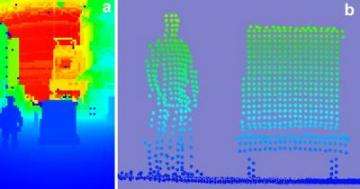
Robots running amok and destroying property may be a staple in science fiction films, but they aren't welcome in factories, warehouses and other places where automatic guided vehicle (AGV) forklifts are used. Under a cooperative research and development agreement with Transbotics, a Charlotte, N.C., AGV manufacturer, the National Institute of Standards and Technology is developing advanced sensor processing and modeling algorithms to help robot forklifts verify the location and orientation of pallets laden with goods.
The experimental system utilizes two onboard, single scan-line LADAR devices to negotiate obstacles and hone in on warehouse pallets. (LADAR--Laser Detection and Ranging--is an optical technology which measures properties of scattered laser light to find range and other information about a distant target.) One LADAR device, located at the base of the AGV, is used as a safety sensor to detect obstacles such as humans in the forklift's path. It also can be used to scan inside a truck's cargo area to detect the presence of a pallet or define distances from the forklift to the truck's inside walls.
The other sensor, called the Panner, is a panning laser ranger mounted on a rotating motor at the top front of the AGV. The Panner acquires many scan lines of range data that allows the scene in front of the device to be reconstructed in various visual formats such as a pseudo-colored coded image (where colors indicate relative proximity to an object) or a 3-dimensional data point "cloud." A computer model is then derived from the data with the output sent immediately to the AGV's control center. This allows the robot forklift to maneuver, load and unload pallets, verify the remaining space within the truck being loaded, and track the number of pallets still needing handling.
The research team recently presented the results of its visualization program at the SPIE Optics East 2006 Conference in Boston.* Transbotics is planning to implement the NIST pallet verification software on one of its AGVs in 2007 for use in real manufacturing situations.
* R. Bostleman, T. Hong and T. Chang. Visualization of Pallets. Presented at the SPIE Optics East 2006 Conference. October 2006 (published online Oct. 2, 2006).
Source: NIST