May 5, 2015 report
Novel catalyst used to make styrene in one step
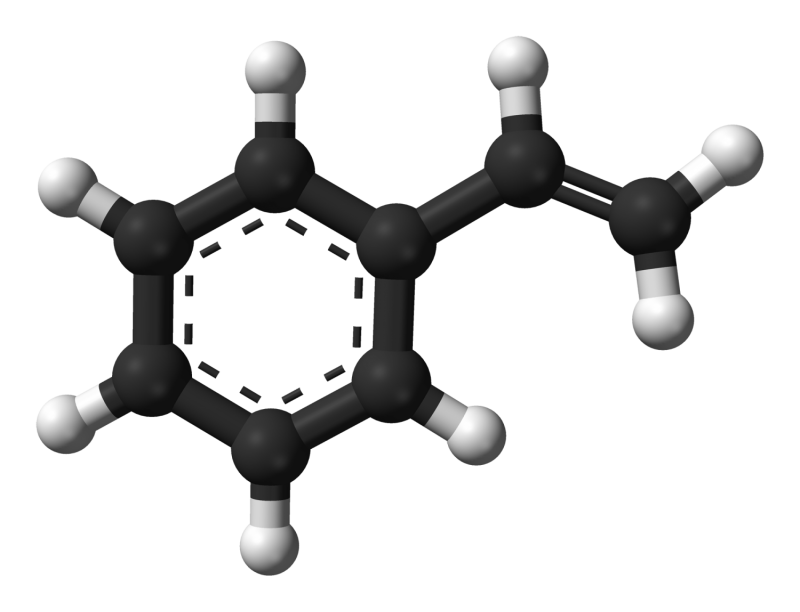
(Phys.org)—Styrene is an important industrial chemical. It is the precursor to polystyrene which is used in various every day plastic products, like disposable cups, packaging, and insulation. Over 18.5m tons of styrene is produced industrially around the world. Typically, styrene synthesis begins with benzene and ethylene, and involves a multi-step process under harsh reaction conditions and often leads to unwanted by-products.
In research that aims to streamline and optimize styrene synthesis Benjamin A. Vaughan, Michael S. Webster-Gardiner, Thomas R. Cundari, and T. Brent Gunnoe from the Department of Chemistry at the University of Virginia and the Center for Advanced Modeling in the Department of Chemistry at the University of North Texas have devised a single-step synthesis of styrene using a novel rhodium catalyst. Their work appears in Science.
The production of styrene, or vinyl arenes in general, involves benzene alkylation. This is typically done under harsh conditions involving high temperatures and either a Friedel-Crafts or zeolite catalyst. This process typically involves poly-alkylated bi-products. Additionally, the alkyl substituent will then need to be oxidized to form the vinyl group, which is usually accomplished with a metal oxide at high temperatures. The products are the target vinyl arene and hydrogen gas, as well as any bi-products from poly-alkylation. Products from poly-alkylation are converted to ethylbenzene in a trans-alkylation step, which follows the alkylation reaction.
Prior research from this group, found that this synthetic process can be streamlined using a platinum catalyst for the alkylation of benzene, and the alkyl group will subsequently undergo beta-hydride elimination, forming free styrene. However, this process degrades the platinum catalyst, likely because the platinum ion further reduces to platinum metal during the beta-elimination phase of the reaction.
To make this one-step process industrially feasible, they need to find an optimal catalyst. Ideally, this catalyst would directly vinylate the benzene ring rather than initial alkylation followed by oxidation of the alkyl group. Additionally this catalyst would not lead to multiple side reactions and have a high turnover number even in harsh oxidative conditions and in the presence of highly reactive metal hydrides. Furthermore, industrially favorable mechanisms would involve recovering and recycling the oxidant using air or oxygen.
For this paper, Vaughan et al. designed a catalyst with rhodium rather than platinum in hopes that the less favorable reduction of Rh(I) to elemental rhodium compared to the reduction of Pt(II) would maintain the integrity of the catalyst.
Prior work in designing a rhodium-based catalyst for a reaction that has a similar carbon-hydrogen activation step was adapted with an ethylene coordinated to the rhodium complex. The ligand framework likely serves to protect rhodium from oxidative damage and may serve other important functions in the mechanism. With this ligand serving to protect the metal, they decided to use a Cu(II) salt as an oxidant because there is precedent for the recovery of Cu(I) and re-oxidizing it to obtain Cu(II), thus enabling the possibility of recycling the oxidant.
Testing of their catalyst with Cu(OAc)2 at 150oC in benzene led to 58 to 62 turnovers in twenty-four hours. Characterization showed high selectivity for styrene, and the copper salt as the limiting reagent. The reaction was optimized by testing various copper salts, temperatures, and concentration of ethylene gas. Cu(OAc)2, while it causes a slower reaction rate than other copper salts, provided a more stable reaction process. Additionally, while the reaction rate did increase with increasing temperature, the catalyst degraded when the temperature was above 180oC. Finally, the reaction rate increased as ethylene pressure was increased.
The optimized reaction conditions provided a near-quantitative yield of styrene with a large turnover number for the catalyst, and the catalyst maintained its integrity for up to 96 hours. The best turnover number observed was at least 800. Kinetic studies showed that this reaction appears to be first-order with respect to ethylene concentration, which is unique to this particular catalyst. Additional kinetic studies revealed that there is a kinetic isotope effect with kH/kD ~ 3.1, which is consistent with other transition metal-mediated C-H activation reactions.
While further studies need to be done to analyze the reaction mechanism, this paper provides a framework by which a novel rhodium complex allows for a one-step reaction to form styrene from benzene and ethylene.
More information: "A rhodium catalyst for single-step styrene production from benzene and ethylene" Science DOI: 10.1126/science.aaa2260
ABSTRACT
Rising global demand for fossil resources has prompted a renewed interest in catalyst technologies that increase the efficiency of conversion of hydrocarbons from petroleum and natural gas to higher-value materials. Styrene is currently produced from benzene and ethylene through the intermediacy of ethylbenzene, which must be dehydrogenated in a separate step. The direct oxidative conversion of benzene and ethylene to styrene could provide a more efficient route, but achieving high selectivity and yield for this reaction has been challenging. Here, we report that the Rh catalyst (FlDAB)Rh(TFA)(η2–C2H4) [FlDAB is N,N′-bis(pentafluorophenyl)-2,3-dimethyl-1,4-diaza-1,3-butadiene; TFA is trifluoroacetate] converts benzene, ethylene, and Cu(II) acetate to styrene, Cu(I) acetate, and acetic acid with 100% selectivity and yields ≥95%. Turnover numbers >800 have been demonstrated, with catalyst stability up to 96 hours.
Journal information: Science
© 2015 Phys.org