Explainer: the science of fireworks
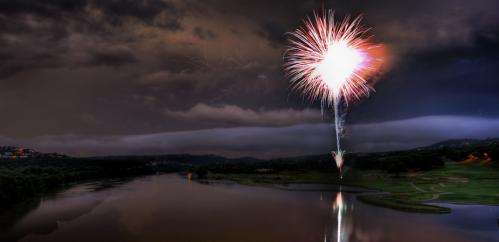
While large firework displays have become even more more popular over the past ten years or so, most of the chemistry behind these exuberant displays has been known for centuries. Marrying this with modern digital technology provides the fiery choreography of our New Year celebrations.
Colours and flames
The school chemistry lesson of "flame colours" provides the clue to how fireworks can provide a range of hues. Metal salts are combined with a fuel and an oxidiser into small balls about the size of a Malteser. When an effect bursts, these burning balls ("stars") of material are flung across the sky and the different metals produce different colours. Strontium provides a red, barium produces green and copper produces blue.
The light is emitted as atoms of these metals absorb heat from the combustion and their electrons are "pushed" further from the nucleus. These electrons then fall back to their original position, throwing out the energy as light. By combining these metals together, a wide range of colours can be made. The past couple of years have seen manufacturers producing more pastel colours of aqua and turquoise. This is most definitely an art form and the recipes are closely guarded commercial secrets.
White is generated using magnesium, aluminium or an alloy of these two as the fuel. These metals burn with an intense white light which can be seen miles away. Some effects incorporate additional materials which subtly modify the burning reaction so it switches itself on and off. This results in strobing effects or twinkling "weeping willows".
Devices
Getting effects into the air is done using the oldest pyrotechnic mixture: gunpowder. While we know this propellant works by accelerating the burning of charcoal by using solid potassium nitrate to provide the oxygen, this ancient composition still holds some secrets.
Small devices are used to provide effects at a low level and the manufacturer will have already placed the effect on top of an amount of gunpowder (the "lift charge") which will also ignite the effect. This is supplied in a cardboard tube to direct the projectile. These devices are not so different to the ones in boxes of garden fireworks, but bigger. "Single shot" devices like these provide the ultimate in variety, but manufacturers also provide compound devices in which lots of single shots are fired from a single fuse to provide sequences of effects that fan across, or provide a sub-display of their own.
The material that is seen higher in the sky is launched differently. These "shells" arrive as spherical or cylindrical projectiles with the lift charge attached underneath in a paper bag. For launching, these are slid down a mortar tube (usually made of a glass fibre composite), with the long fuse coming out of the top. The mortar tubes are usually held in racks, staked into the ground, or otherwise securely held in place.
Choreography and control
All but the smallest displays are fired electrically. While garden fireworks have a fuse designed to burn slowly, display fireworks have the opposite. This fuse is made of the appropriately named "quickmatch" and into the centre of this an igniter is placed. This is then wired into a panel with a channel for each cue. The panel is linked to a laptop (or similar) which is pre-programmed with the display.
At the right moment, the laptop sends the command to the panel, which gives off an intense electrical pulse, the igniter bursts into flame and the quickmatch passes the heat to the firework which launches. All this happens in the blink of an eye. A large display may contain more than 500 cues (many firing multiple devices) and the speed of response is vital if the display is choreographed to music.
Setup
The design work for a display will start weeks, maybe months before the event. Software allows a designer to see what the display will look like in real time and can incorporate important features such as buildings and trees, or additional elements like lights and lasers. The software also prints out tables showing which devices need to be wired into which channels on which panel.
On the day, teams of people arrive at the launch site and set up racks of mortar tubes and other equipment designed to hold devices at the correct angles to provide traces that fan, cross over and so on. Once the framework is in place, wiring devices takes place, followed by weatherproofing and checking. A recent large display I was involved in required ten people working from 10am for an 8pm launch of a 20 minute display.
So as you watch the sky light up to see out the old year and bring in the new, remember that what you see depends upon both old and new too.
Provided by The Conversation
This story is published courtesy of The Conversation (under Creative Commons-Attribution/No derivatives).