April 7, 2009 feature
Carbon Nanotubes Toughen a Common Plastic
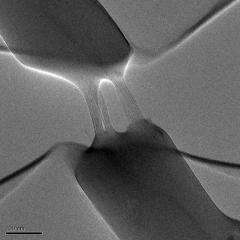
(PhysOrg.com) -- A research group from the Weizmann Institute of Science in Israel has discovered that adding carbon nanotubes to a widely used commercial plastic can greatly strengthen it. Their work is one example of how incorporating carbon nanotubes into plastics and other materials can yield composites with much improved properties.
The plastic, known as PMMA, is most commonly used to make shatterproof glass-substitute materials, such as the brands Plexiglas and Lucite. The researchers reinforced PMMA fibers with both single-walled and multi-walled carbon nanotubes and found that, while both types were effective, the highest toughness was achieved with the multi-walled nanotubes, which resemble several single-walled nanotubes nested together.
Bulk materials reinforced with nanostructures are the future of composite materials, beginning to replace composites made with micrometer-sized particles. Carbon nanotubes are a natural choice because they are exceptionally strong, and the multi-walled varieties are especially tough because of their more complex structures; they can contain up to 50 nested nanotubes.
But achieving significant improvements in a material's strength via nanotube reinforcement doesn’t happen often because of hard-to-avoid issues like nanotube clustering—some nanotubes randomly aggregate rather than distribute evenly. This may even reduce a material's strength.
“Despite the large numbers of studies being done, there are still contradictory findings on the role of carbon nanotubes as reinforcement agents and the role of nanotube type—multi-walled versus single-walled—has not been adequately addressed,” said the study's lead scientist, H. Daniel Wagner, to PhysOrg.com.
He continued, “Another major challenge in preparing nanocomposites is developing procedures that distribute nanostructures in ordered ways. We used electrospinning, which is both simple and effective in creating large-scale nanocomposite materials.”
Electrospinning involves using an electric charge to draw very fine fibers or structures (typically on the micro- or nanoscale) from a liquid and deposit them elsewhere. It is used in many areas of science and technology, from making textiles to creating components for artificial organs.
Wagner and colleague Xiaomeng Sui electrospun both pure PMMA fibers and fibers reinforced with either single-walled carbon nanotubes (SWCNTs) or multi-walled carbon nanotubes (MWCNTs). Their analysis shows that the nanotubes embedded among the fibers were nicely aligned along the fiber axis. The SWCNTs formed long, thick ropes, which turn out to triple the composite's toughness. The MWCNTs, on the other hand, were more evenly dispersed, leading to even larger toughness enhancements.
Wagner and Sui tested each composite's strength using a “nanotensile” device they designed, which stretched the fibers until they broke. They watched the process under an electron microscope. To eliminate the effect of fiber diameter on the results, they limited their scope to samples with diameters between 500 and 750 nanometers.
The addition of carbon nanotubes to the PMMA fibers causes a “striking” transformation, they found. The pure PMMA fibers developed thin “necks” and broke under relatively small strains. Both composites also experienced necking, but only failed at strain values that were comparatively enormous. That is, they deformed but did not break under much more forceful stretching than that applied to the pure fibers.
Theses findings are published in the March 2, 2009, online edition of Nano Letters.
Citation: Nano Lett., Article ASAP DOI: 10.1021/nl803241y
Copyright 2009 PhysOrg.com.
All rights reserved. This material may not be published, broadcast, rewritten or redistributed in whole or part without the express written permission of PhysOrg.com.