Nanocoatings boost industrial energy efficiency
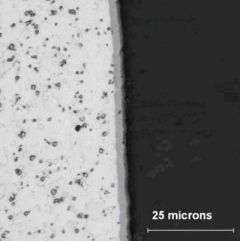
Friction is the bane of any machine. When moving parts are subject to friction, it takes more energy to move them, the machine doesn't operate as efficiently, and the parts have a tendency to wear out over time.
But if you could manufacture parts that had tough, "slippery" surfaces, there'd be less friction, requiring less input energy and the parts would last longer. Researchers at the U.S. Department of Energy's (DOE) Ames Laboratory are collaborating with other research labs, universities, and industrial partners to develop just such a coating.
"If you consider a pump, like a water pump or a hydraulic pump, it has a turbine that moves the fluid," said Bruce Cook, an Ames Laboratory scientist and co-principal investigator on the four-year, $3 million project. "When the rotor spins, there's friction generated at the contacting surface between the vanes and the housing, or stator. This friction translates into additional torque needed to operate the pump, particularly at start-up. In addition, the friction results in a degradation of the surfaces, which reduces efficiency and the life of the pump. It takes extra energy to get the pump started, and you can't run it at its optimum (higher speed) efficiency because it would wear out more quickly."
Applying a coating to the blades that would reduce friction and increase wear resistance could have a significant effect in boosting the efficiency of pumps, which are used in all kinds of industrial and commercial applications. According to Cook, government calculations show that a modest increase in pump efficiency resulting from use of these nanocoatings could reduce U.S. industrial energy usage by 31 trillion BTUs annually by 2030, or a savings of $179 million a year.
The coating Cook is investigating is a boron-aluminum-magnesium ceramic alloy he discovered with fellow Ames Laboratory researcher and Iowa State University professor of Materials Science and Engineering Alan Russell about eight years ago. Nicknamed BAM, the material exhibited exceptional hardness, and the research has expanded to include titanium-diboride alloys as well.
In many applications it is far more cost effective to apply the wear-resistant materials as a coating than to manufacture an entire part out of the ceramic. Fortunately, the BAM material is amenable to application as a hard, wear-resistant coating. Working with ISU materials scientist Alan Constant, the team is using a technique called pulsed laser deposition to deposit a thin layer of the alloy on hydraulic pump vanes and tungsten carbide cutting tools. Cook is working with Eaton Corporation, a leading manufacturer of fluid power equipment, using another, more commercial-scale technique known as magnetron sputtering to lay down a wear-resistant coating.
Pumps aren't the only applications for the boride nanocoatings. The group is also working with Greenleaf Corporation, a leading industrial cutting tool maker, to put a longer lasting coating on cutting tools. If a tool cuts with reduced friction, less applied force is needed, which directly translates to a reduction in the energy required for the machining operation.
To test the coatings, the project team includes Peter J. Blau and Jun Qu at one of the nation's leading friction and wear research facilities at DOE's Oak Ridge National Laboratory, or ORNL, in Tennessee. Initial tests show a decrease in friction relative to an uncoated surface of at least an order of magnitude with the AlMgB14-based coating. In preliminary tests, the coating also appears to outperform other coatings such as diamond-like carbon and TiB2.
In a separate, but somewhat related project, Cook is working with researchers from ORNL, Missouri University of Science and Technology, the University of Alberta, and private companies to develop coatings in high-pressure water jet cutting tools and severe service valves where parts are subject to abrasives and other extreme conditions.
"This is a great example of developing advanced materials with a direct correlation to saving energy," Cook said. "Though the original discovery wasn't by design, we've done a great deal of basic research in trying to figure out the molecular structure of these materials, what gives them these properties and how we can use this information to develop other, similar materials."
Source: Ames Laboratory