Engineers Develop New Way to Tailor Polymer Coatings
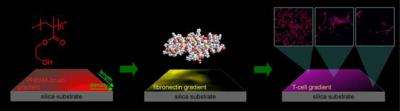
Which polymer coating works best on contact lenses and which is more appropriate for the creation of artificial organs via tissue engineering? In the past the process for selecting the correct structure was a trial-and-error guess, given the myriad possibilities based on numerous polymer properties such as chain length and density.
At North Carolina State University chemical engineers have developed a way to take the guessing game out of the development of polymer coatings. Using a single substrate to grow a polymer scaffold, they created a test bed that can be used to explore both clouding of lenses and tissue engineering. Dr. Jan Genzer, associate professor of chemical engineering, and Rajendra Bhat, a former postdoctoral researcher in Genzer’s group, used their novel substrate to tailor adsorption of proteins and adhesion of bone-forming cells - two important phenomena involved in clouding of lenses and tissue engineering. The result of their research appears in the December issue of the journal Advanced Materials. A graphic image depicting the research appears on the journal cover.
Genzer and Bhat created a technique for growing polymers on a substrate such that polymer gets more sparse (less dense) in one direction and increases in molecular weight (or length) in another direction. The result is a substrate with a polymer scaffold that has the unique quality of having every different combination of density and molecular weight.
“We created a unique type of substrate known as orthogonal gradient that allows two different properties of the grafted polymer chains, namely the grafting density and chain length, to vary independently in two perpendicular directions,” says Bhat. “Since these two properties are changing continuously across the substrate, every possible combination of the two properties can be probed systematically.”
“This chemistry is not new,” says Genzer. “It is just re-engineering. It allows us to test what is the right combination of molecular weight and density of a polymer for a particular condition to exist. At one point the combination may attract proteins while another point may prevent protein adhesion.”
Genzer and Bhat used poly (hydroxyethyl methacrylate), PHEMA, a common polymer coating used on contact lenses to prevent clouding from protein adhesion. Once they created the orthogonal gradient of PHEMA on a silicon chip or a glass substrate, they studied the accumulation of proteins and then cells. They observed that on those parts of the substrate that have the longest polymer chains grafted at the maximum density the protein adhesion was minimal. On the other hand, abundant protein adhesion was noticed when polymer chain length as well as grafting density was at their least value. Upon culturing cells on such a substrate, the number density as well as shape of the cells showed gradual variation across the substrate, indicating different levels of compatibility with the substrate. Having a good control over compatibility of cells with an artificial device is of great significance in designing implants and prosthetic devices.
Their process for growing PHEMA across a substrate at varying densities and molecular weights will revolutionize the way polymer coatings are selected for specific applications by allowing researchers an easy way to test complex processes. One important feature is the ability to test any polymer, thus expanding the range of applications impacted by Genzer’s technique. The technology will be most important to both the marine and healthcare industries since both industries are interested in the processes of biofouling, which is the adhesion of proteins and cells to a surface.
“Due to the large number of parameters controlling protein adsorption, it is not easy to study biofouling,” says Bhat. “But our novel polymer gradient substrates greatly improve the process.”
For example, with contact lenses, manufacturers and wearers want to have the best antifouling coating possible. An antifouling coating is what keeps the proteins in the eye from adhering to the contact lens material. It is the accumulation of proteins on the surface of the contact lens that creates the cloudiness that makes the lenses unusable. Using the technique developed by Genzer and Bhat, contact lens developers can test an infinite number of unique polymer configurations to find the best antifouling coating specifically for contact lenses.
In the area of tissue engineering, researchers may be looking for the opposite properties and want the polymer to attract proteins and cells so that artifical tissues can be built around the polymer scaffold. Genzer and Bhat’s technique can be used to determine what polymers are best at attracting particular proteins thereby eliminating the guessing game in the development of implants and prosthetics.
In addition to helping researchers develop the best medical products for a variety of uses, the technique will greatly reduce the cost of research and development of these products since the polymer selection process can be streamlined.
The process will also help improve fuel efficiency in the shipping industry. In the marine industry, biofouling — the adhesion of marine organisms to the hulls of ships — costs millions of dollars in lost fuel efficiency due to the drag created by the organisms attached to ships’ hulls. Adding to the cost of biofouling is the expensive process of removing the organisms and repainting. Using the new technique for testing polymer coatings, researchers can select the best coating for ships’ hulls.
“The polymer gradient substrate allows researchers to easily determine the amount of proteins and cells that will attach to a particular polymer surface,” says Genzer. “The result is that we have better medical devices that will last longer in the body and better fuel economy for the shipping industry.”
Source: North Carolina State University