Nano-Armor: Protecting the Soldiers of Tomorrow
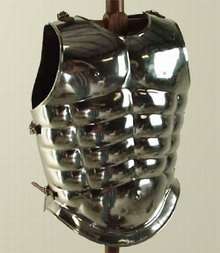
An Israeli company has recently tested one of the most shock-resistant materials known to man. Five times stronger than steel and at least twice as strong as any impact-resistant material currently in use as protective gear, the new nano-based material is on its way to becoming the armor of the future.
Above: Illustration photo - medieval armor. The discovery of the extraordinary wave-shock absorption quality of the IF materials, position it as one of the best candidates for future protective gear and armor.
A year ago IsraCast reported on the development of the first commercial nano-based lubricant which was developed by the Israeli company ApNano materials. A year later we find ApNano working also on a wholly different application of their technology - shielding and protection. In recent research lead by Prof. Yan Qiu Zhu of the School of Mechanical, Materials and Manufacturing Engineering at the University of Nottingham, England, a sample of the ApNano material was subjected to severe shocks generated by a steel projectile traveling at velocities of up to 1.5 km/second. The material withstood the shock pressures generated by the impacts of up to 250 tons per square centimeter. This is approximately equivalent to dropping four diesel locomotives onto an area the size of one’s fingernail. During the test the material proved to be so strong that after the impact the samples remained essentially identical compared to the original material. Additionally, a recent study by Prof. J. M. Martin from Ecole Central de Lyon in France tested the new material under isostatic pressure and found it to be stable up to at least 350 tons/cm2.
In the line of fire - creating super shock-resistant materials
In order to understand how it is possible to create this ultra-strong shock absorbing material we first need to understand the nature of the nano material developed by ApNano. In the early 1990's the Nano-materials Synthesis Group in the Weizmann institute headed by Professor Reshef Tenne, ApNano Chief Scientific Advisor, and recent winner of the Materials Research Society medal, together with Dr. Menachem Genut, currently the President and CEO of ApNano Materials, Prof. Gary Hodes and Dr. Lev Margulis, discovered a new class of inorganic nanostructures.
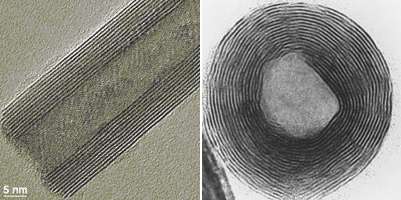
The group had found that certain inorganic compounds such as WS2, MoS2, TiS2 and NbS2 that normally occur as large flat platelets can be synthesized into much smaller nano-spheres and nano-tubes which they named inorganic fullerene-like nanostructures or IF for short. Fullerenes are a new form of carbon, other forms being diamond, graphite and coal. They are molecules composed entirely of carbon, taking the form of a hollow sphere, ellipsoid, or tube. Spherical fullerenes are sometimes called buckyballs, while cylindrical fullerenes are called buckytubes or nanotubes. Buckyballs are named after R. Buckminster Fuller, architect of the geodesic dome that he designed for the 1967 Montreal World Exhibition. IF materials are Fullerene-like materials but instead of being composed out of carbon they can be created from various other inorganic elements.
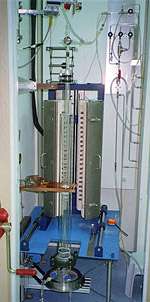
Currently ApNano can manufacture only a few kilograms of the new material a day at their lab in Nes Ziona. In an interview by IsraCast, Dr. Menachem Genut, ApNano CEO, explained that the company is moving into semi-industrial manufacturing within the next six months producing between 100-200 kilograms of the material per day, gradually moving to full-scale industrial production by 2007, creating several tons each day. Although it is currently still hard to determine the exact price of the "nano-armor" when in full industrial production, given the cost of the original materials (Tungsten Disulfide, Titanium Disulfide, etc.) and the relatively low production costs, Dr. Genut stated that a kilogram of the new material will cost considerably less than a similar amount of the carbon-based Fullerenes. More field testing will need to be carried out before the nano-armor can be declared commercial but the company is optimistic that with some external financial backing it will be possible to have the first product ready in less then three years.
by Iddo Genuth - IsraCast
The original story can be found here.
For any comments about this story, please contact the writer of the original article.
© 2005 IsraCast. Published with permission of Iddo Genuth