Tailored materials for lightweight vehicles
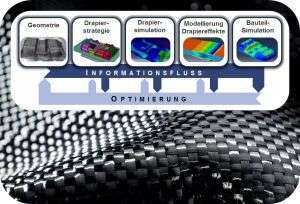
Karlsruhe Institute of Technology (KIT) and the Vector Foundation jointly established the Young Investigator Group (YIG) "Green Mobility – Weight-optimized Vehicle Structures Using Tailored High-performance Fiber Composites". This new Young Investigator Group is aimed at improving the simulation of high-performance fiber composite plastics for the weight-optimized design of vehicle components.
Lightweight vehicles consume less fuel, emit less pollutant, and improve the environmental compatibility of mobility. Lightweight structures are also needed for electric vehicles in order to compensate the relatively high weight of batteries and to save energy. The weight of structural components can be reduced significantly by the use of high-performance fiber composite plastics. These materials consist of a plastic matrix with embedded, extremely thin reinforcing fibers. Thanks to their high specific stiffness and strength, these fibers are ideally suited for lightweight applications.
However, use of high-performance fiber composite plastics is far from being established in automotive engineering. "Among others, this is due to the fact that these materials cannot be simulated accurately enough," explains Dr. Luise Kärger, Head of the new "Green Mobility" YIG of the Chair of Lightweight Technology of the KIT Institute of Vehicle System Technology (FAST). "There still is a considerable difference between the real behavior of high-performance fiber composite plastics, which is influenced significantly by process control and process conditions, and the idealized assumptions of models used for structure simulation." In contrast to metals, stiffness and strength of high-performance fiber composites are influenced by the local fiber architecture. The ultimate fiber architecture of the components results from the draping process. Draping is forming the two-dimensional fiber material into a three-dimensional structure, the so-called pre-form. Its fiber architecture may be very heterogeneous due to different orientations and permeability of the fibers and different forms and structures of fiber bundles. But also local effects, such as overlaps, gaps, and fiber waviness, play a role. "Vehicle structures made of high-performance fiber composites can only be designed in a weight-optimized way, if the carrying capacity can be predicted with sufficient precision, if orientation dependence of the fibers is utilized to the full extent, and if manufacturing effects are identified correctly and taken into account," Luise Kärger summarizes.
To enhance simulation of high-performance fiber composite plastics, the scientists of the "Green Mobility" YIG work on an efficient draping simulation that predicts the local fiber architecture of the pre-forms with sufficient accuracy. Moreover, they develop appropriate structure mechanics models to describe local draping effects as well as an efficient component simulation that considers all globally relevant effects. By means of the developed methods, the scientists derive approaches to determine the optimal draping strategy for the given component geometries in order to comply with the required capacities of the components and to minimize their weight. The YIG also contributes to the work of the KIT Mobility Systems Center.
Provided by Karlsruhe Institute of Technology